Zimbabwe Trip
Presentation for the John Cameron Travel Trust
By
Hunter Parsons, James Galloway and Lewis Turnbull
Gwaai Tobacco farm
Gwaai farm was established by Andrew Locks Grandfather in 1965, the farm is 900Ha, 400Ha is owned and the rest is rented. In early 2000 a large amount of land was lost during the land reform act. The family is currently renting land from some of the natives and building relationships with them with the intent to buy some of the land back. The farm currently grows 170ha of tobacco and 100Ha of maize, and 120Ha of wheat. And the rest is rough grazing for the cattle enterprise which is an 800 cow suckler herd.
The farm grows its Tobacco for “Northern Tobacco”, the tobacco used to be sold at auction, however after the county’s economy crashed the large tobacco company’s buying the tabaco started financing the farmers with imputes such as fertiliser and seed etc, and applying interest on to these products, this meant that farmers could still grow the crop however the large processing companies had a lot of control over the industry, being able to control the price while it also made it hard for farmers to get out of the tobacco industry.
Power is a large limiting factor for the business, with the current energy crisis and Zimbabwe’s main source of electricity comes from a Hydro on the lake Kariba dam (this hydro is shared with Zambia), the Zimbabwean government has overused the dam depleting their share of the water. This has created a shortage of energy on a national scale, creating an unsustainable source of energy for the country, this is reflected via power cuts, every evening at anytime between 6pm-9pm there is a national power cut, and this will come back on between 4am-6am. The farm is currently running on diesel powered generators overnight, however with rising fuel prices This has created a scope for the farm to move to solar for there power usage.
During our time in Zimbabwe, we were there during the harvest season. The first stage after the crop has grown is “reaping” this involves workers going along and harvesting the biggest leaves of the bottom of the plant. By reaping the bottom leaves every 4 days on average, this enables the tobacco plants to tiller upwards making them more productive.
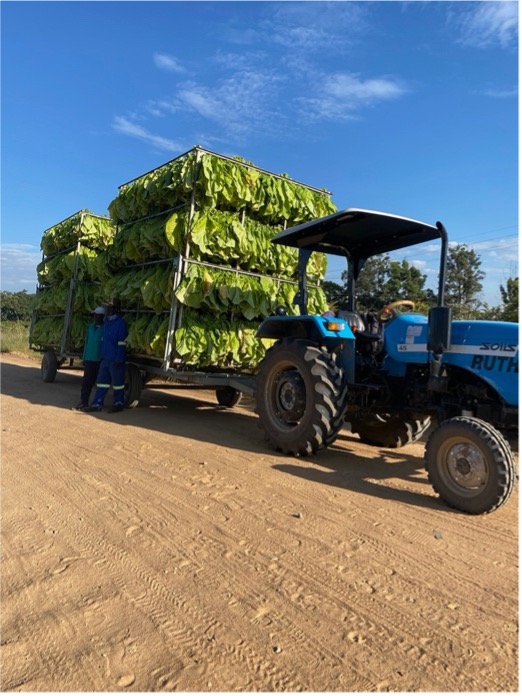
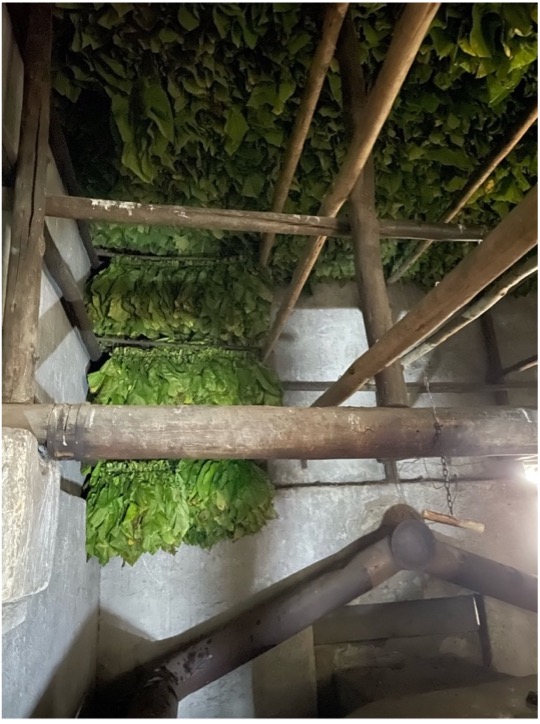
After the plants have been reaped by hand, they are put onto a tractor and trailer as seen in image 1. The tobacco leaves are then transported back to the yard where they are put into curing rooms (image 2) where they are stored for 7 days. This can vairy due to soil types, verities and amount of fertiliser that has been applied. This room heated via coal fires and is kept at about 37 degrees heat, (1kg of coal dry’s 1kg of tobacco). 60% of the moisture in the leaves is lost within the first 3 days of curing.
After 7 days (approximately) the leaves come out of the curing process there are loaded into boxes and taken into the grading shed. when they enter the boxes have steam directly injected (through compressor-like system) into the boxes to keep the moisture in the leaves so they do not tare or crumble. There are 9 – 27 grades of Tabaco leaves and these are graded on the ripeness of the leave, they are graded into bundles. Top leaves are usually best.
Photos from the grading shed.
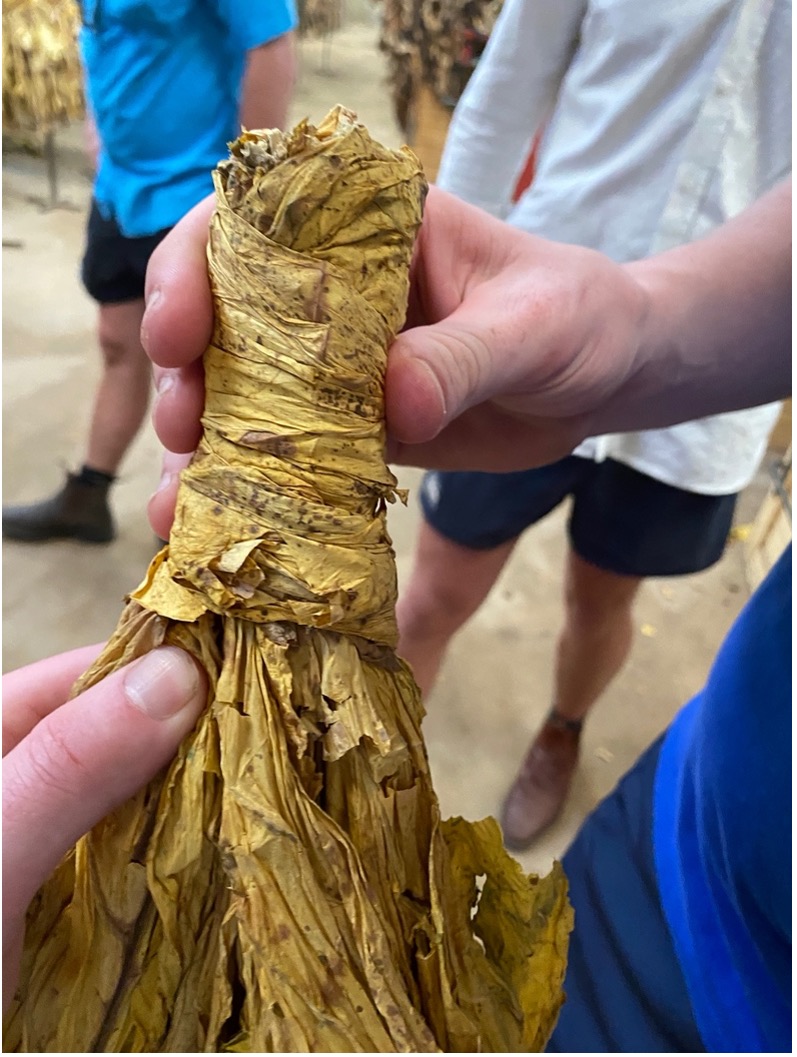
How the bundles are wrapped together.
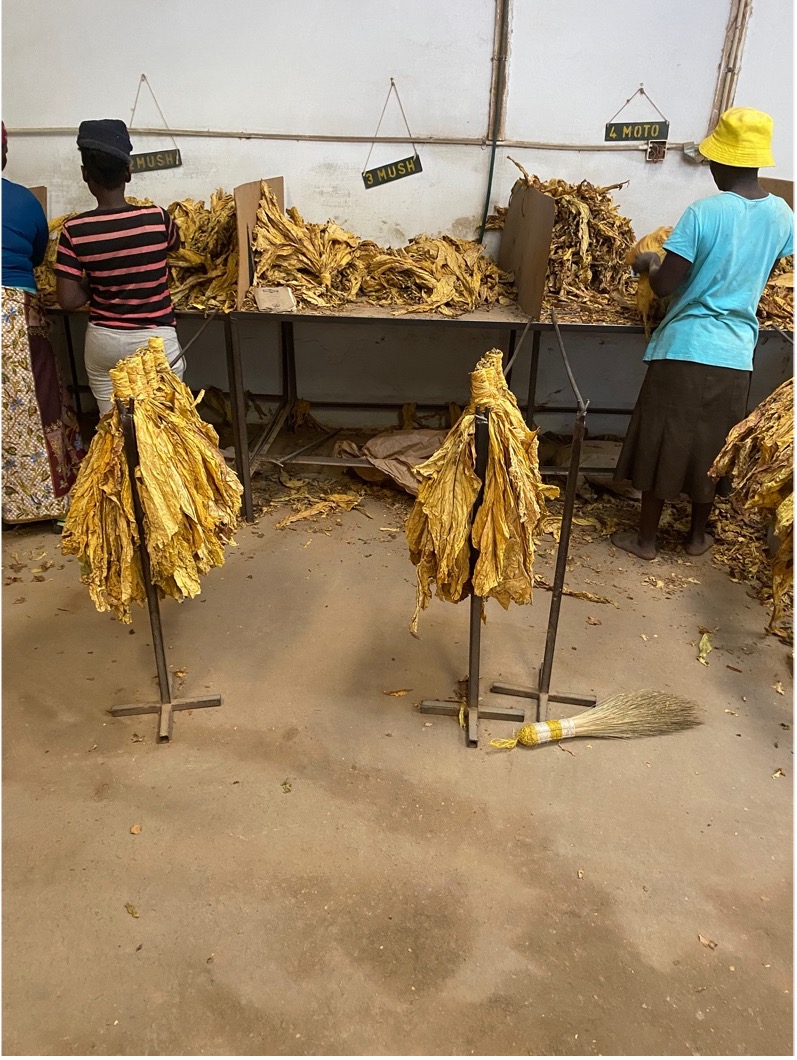
Leaves being graded and then bundles accordingly.
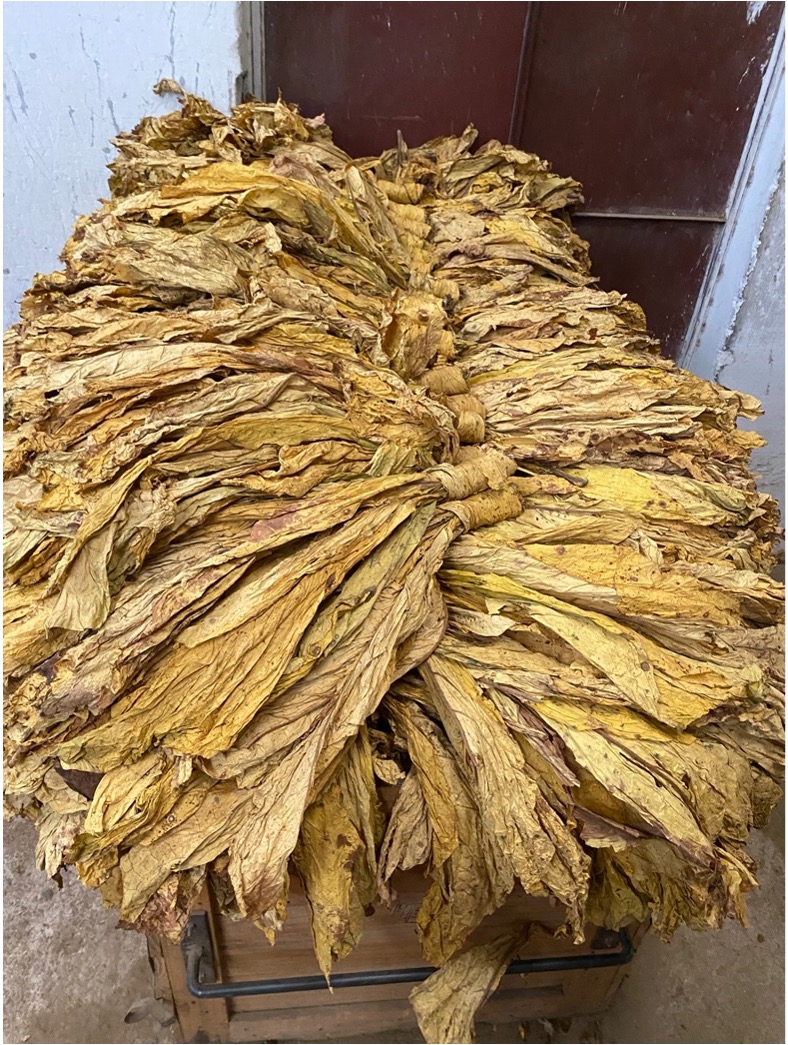
Graded leaves being put into boxes ready to be baled.
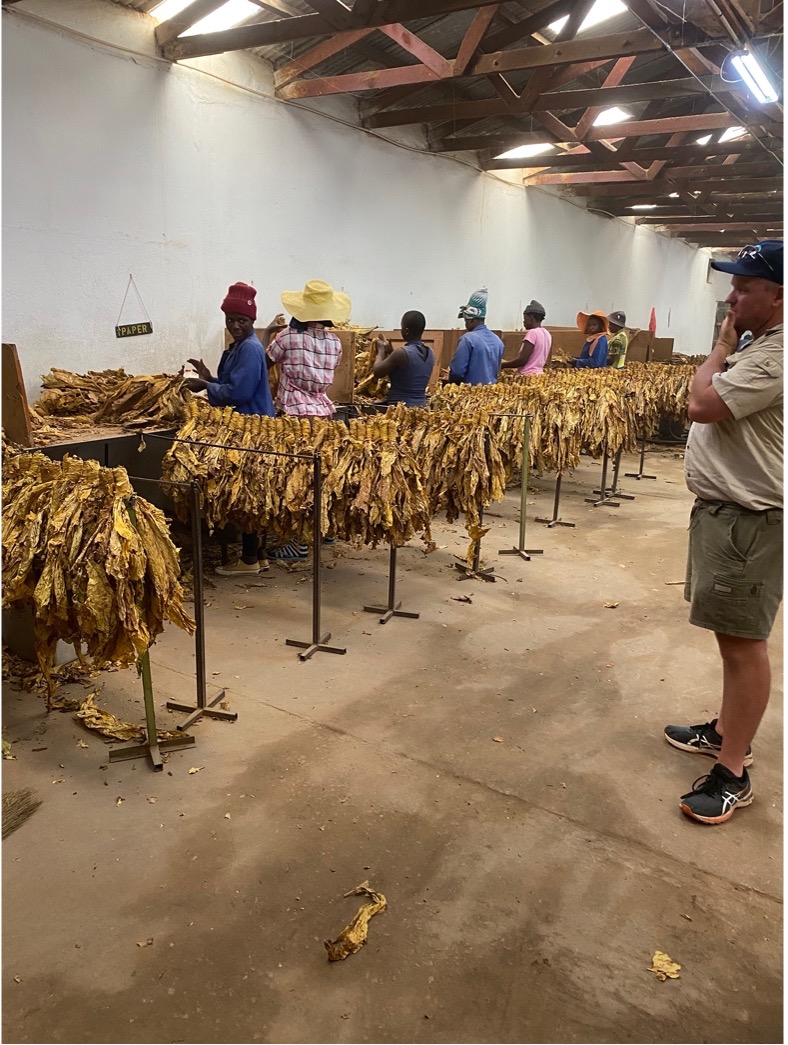
Another photo of the leaves being graded
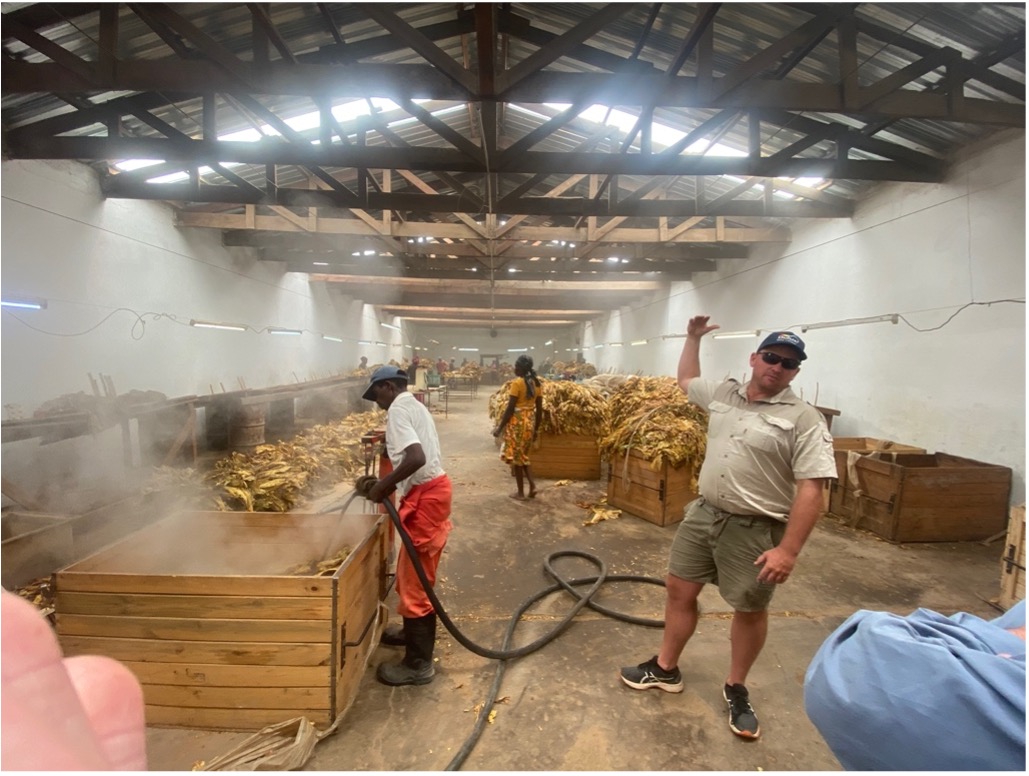
Approximately 4.5t of tobacco passed through the grading shed each day, which equates to 120,000 leaves a day per grader (18 graders). Each bundle of leaves is worth between $1.5 – $4 depending on the grade and quality. Last year the farm averaged $3 a bundle over all their grades. Zimbabwe tobacco is the best quality tobacco in the world, this is due to soil types, but predominantly the climate.
The verity’s and grades the Chinese market want are usually more “lemony” (yellower leaves etc) currently the largest tobacco industry accounting for approximately 40% of the world’s total cigarette consumption. generally, the Chinese market pays better than the European market. Europe generally likes a more orange leaf/variety, this makes it oilier and more flavoursome.
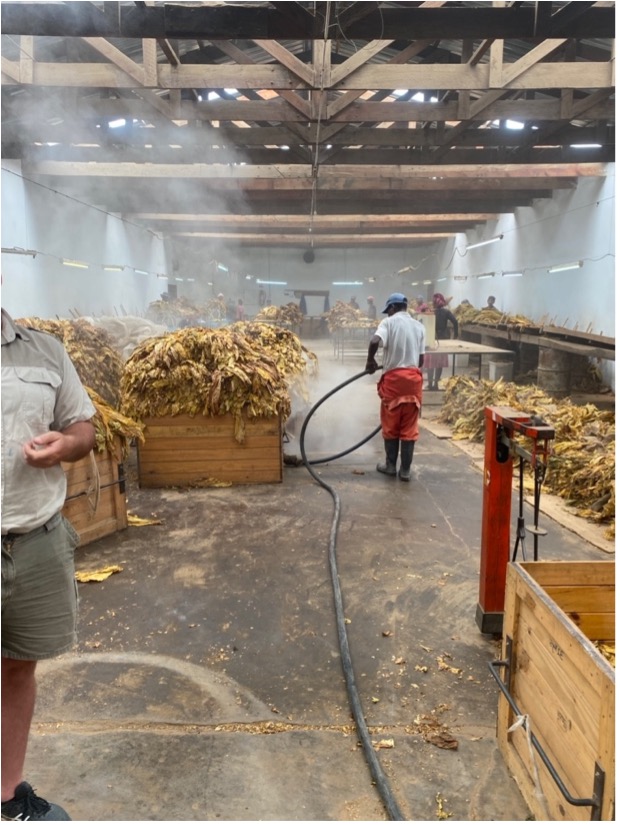
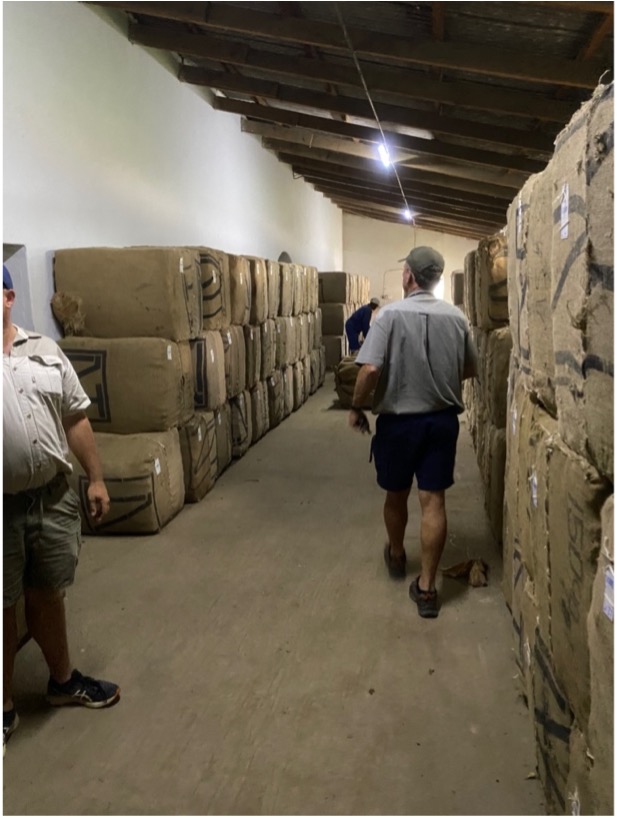
After the overall sale of the cigarettes the actual amount of the overall money the producers get for this is approximately 4% of the total sale, with 50% + of the value being tax. To put this into perspective if you were to buy a £10 packet of cigarettes 40p of that would go to the tabaco producer. Below are some more photos of another curing tunnels we visited that was on another site from the curing sheds, these tunnels are a lot more efficient and commercial than the sheds shown above. When the tobacco plants reach here, they are left to wilt for a day and then they enter the tunnel, Day one they start off at 36 degrees and then they are moved through the tunnel each day gradually building up the temperature, until finally day 7 where they are in a tunnel at 65-70 degrees @ approximately 90% humidity. Some pictures are shown below.
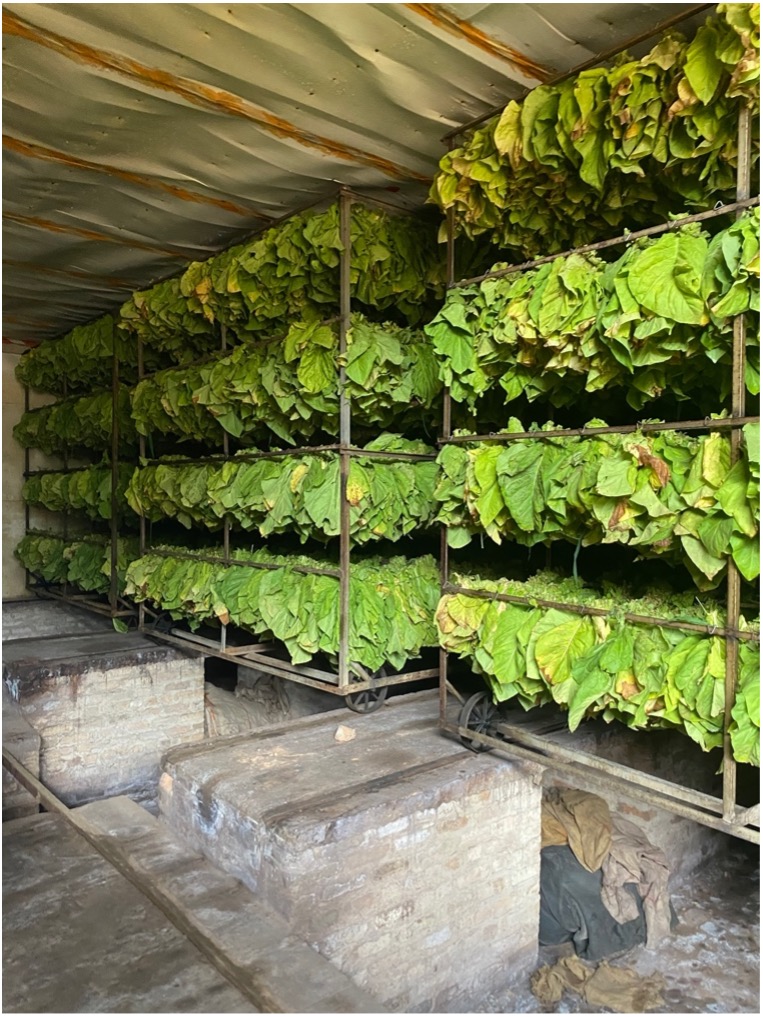
Day 2 – When they enter the tunnel
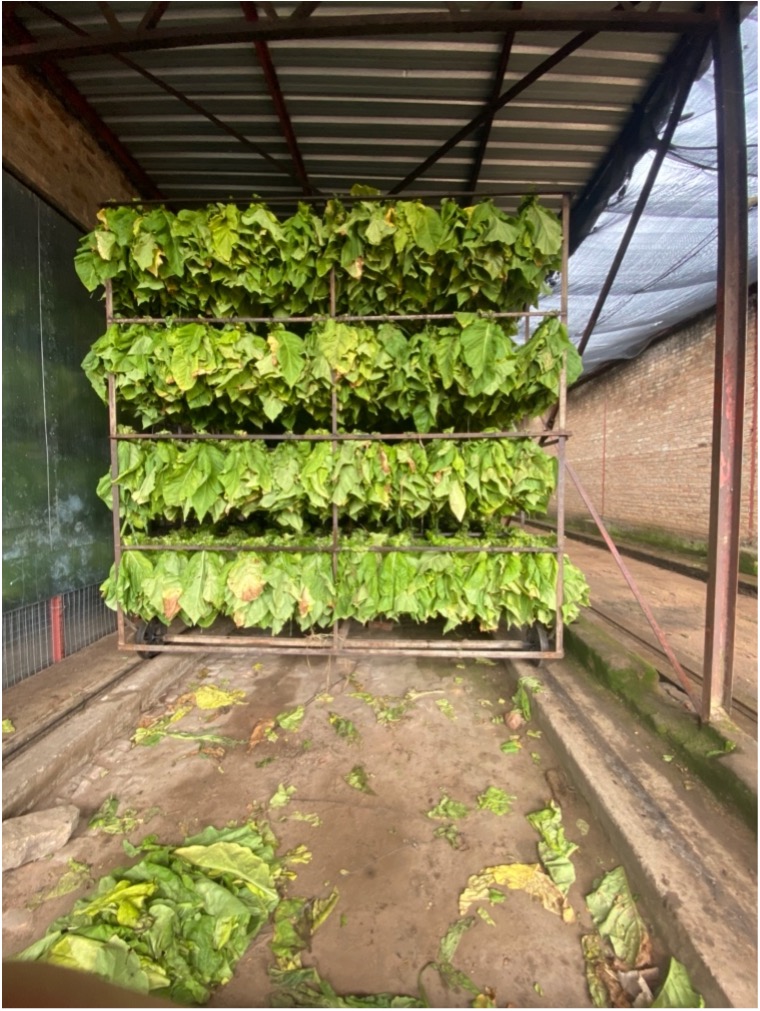
Day one – The Wilting Process
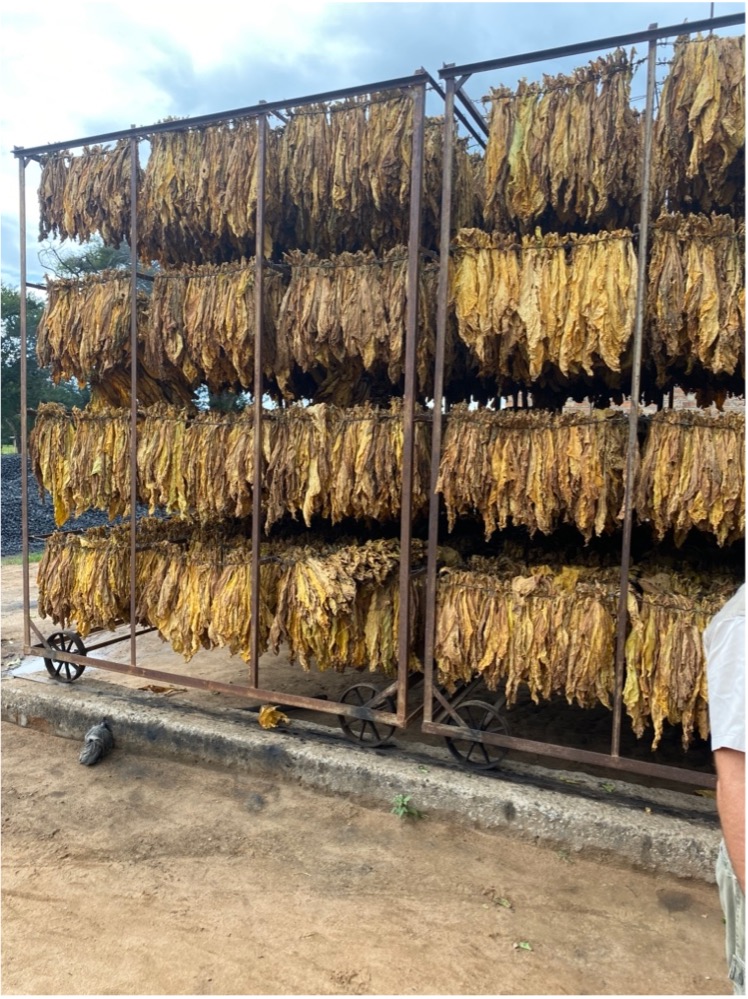
Day 7 – The leaves that have finished the curing process
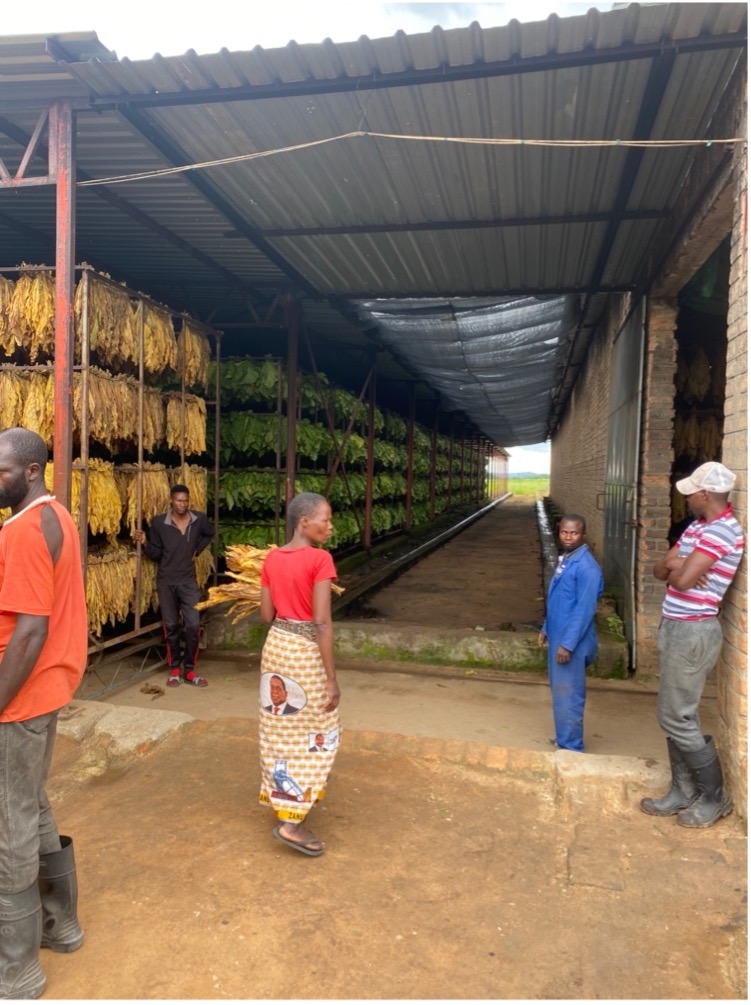
Trolly at the front cured coming out, and all behind wilting process.
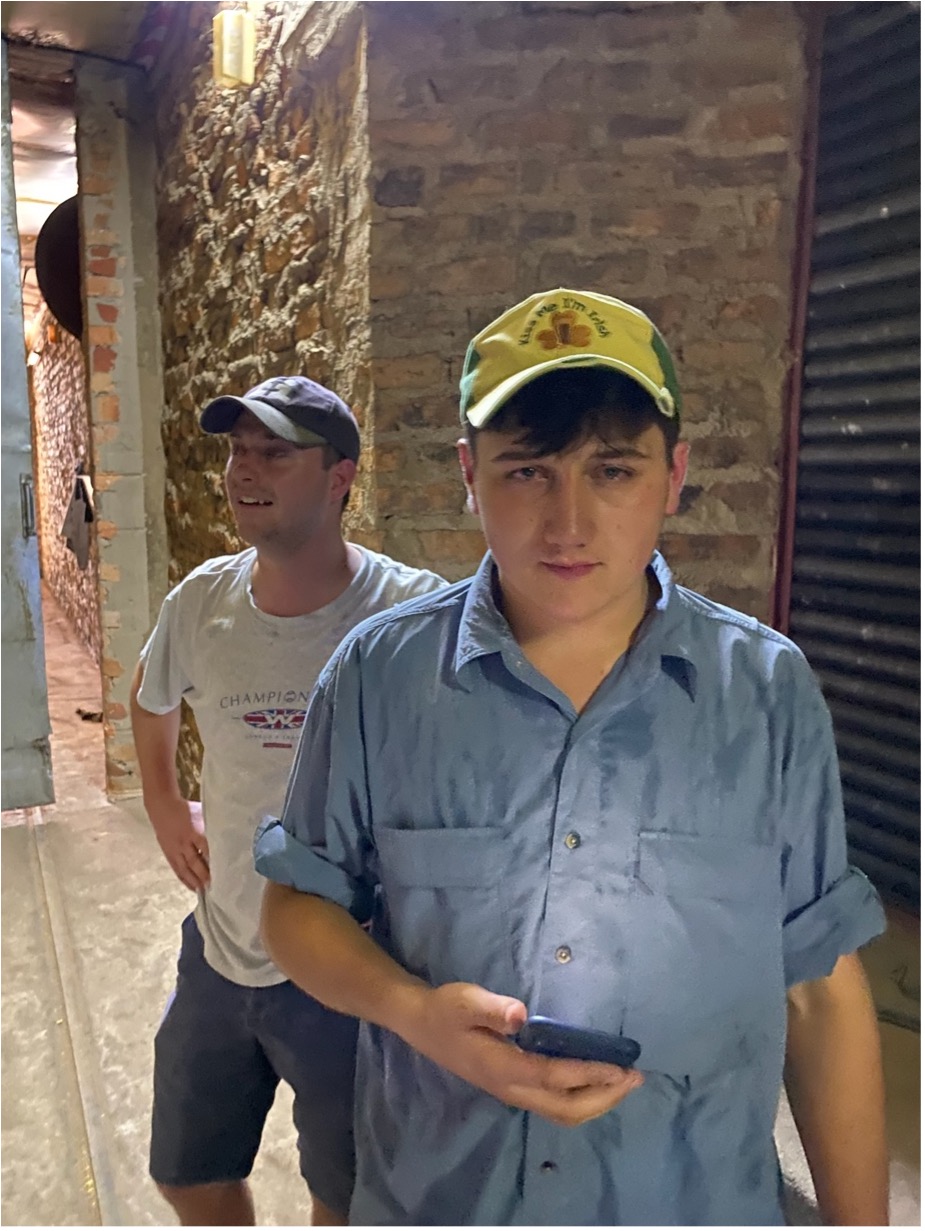
We walked through the tunnels to see what happens on the inside, and you can see from Thomas’s eyes how the nicotine that circulated the tunnel and the heat affected us, this was after about 5-10 minutes of being inside the tunnel, and everyone’s eyes were watering, and everyone was roasting hot, sweating, and due to the heat and humidity, it made you feel as if you could not breath properly.
The natives that work here however have become used to working in these conditions, however when the trolleys are being moved through the tunnels by the workers they usually go in and work for about 30 minutes and then have 10 minutes out again, we could not believe how hard working the natives were.
Blueberries Pinfeilds Farm
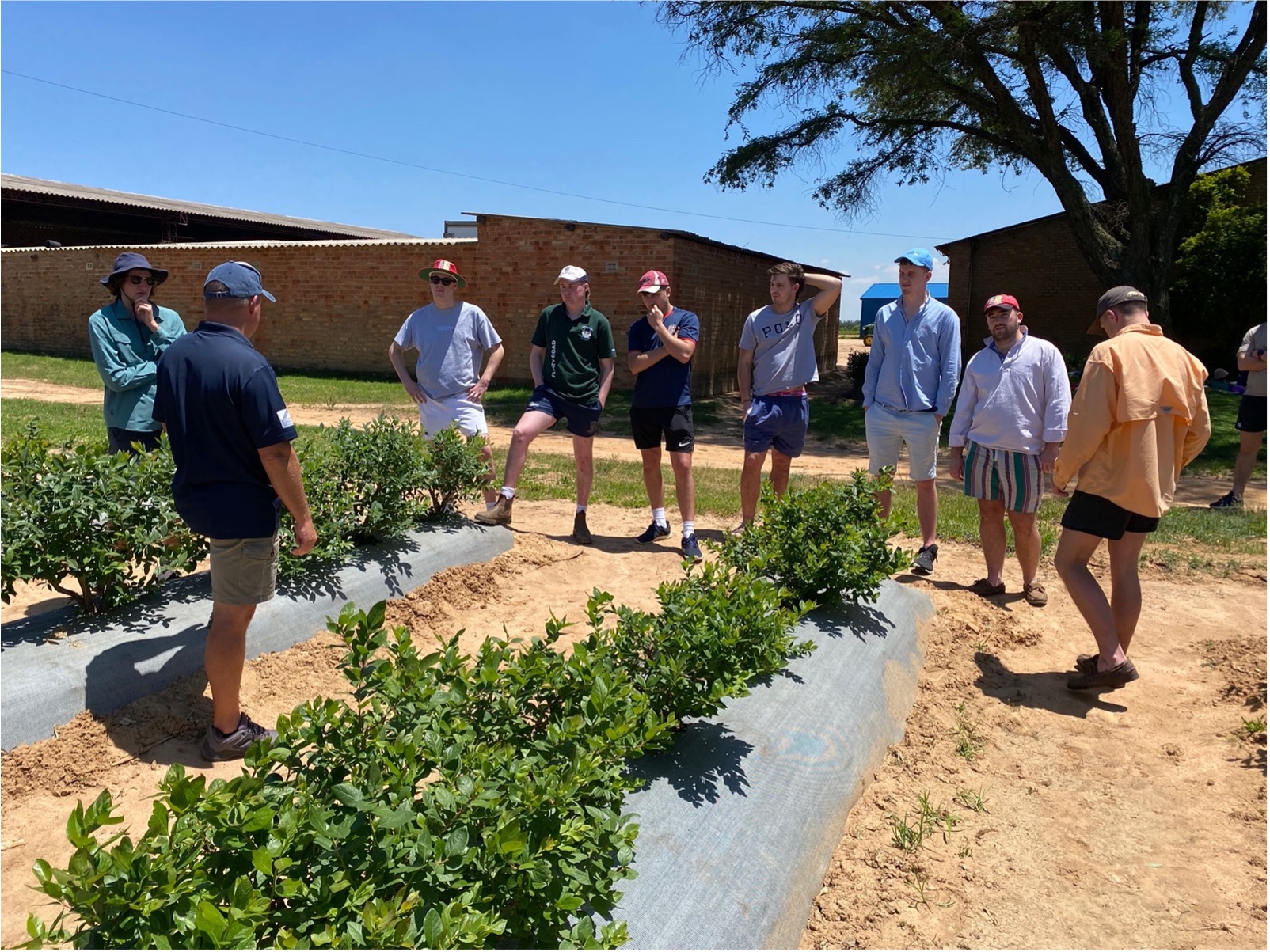
Over the trip in Zimbabwe, we visited 3 different blueberry farms, we were staying at our friend Struan’s house on Hidden Valley Farm, we also went to visit another one of our friend, Marcus’s Philp’s farms about 30 minutes away from Ruwa, this farm is called Foxhill but the main farm we went to see is called Pinfeilds, this is owned by Struan’s family however it is managed by Kelly Bennett. This farm has been farmed by the family for 7 years now.
All the blueberry plants were initially in pots; however, they are all now in beds, this is to reduce the costs of pots, changing the plants from pots to beds reduced their initial cost of production by approximately £60,000 per ha. Pinfeilds was lucky they were able to make this change to beds, due to the fact they have deep sandy loam soil types, without this fee draining soil the blueberries plants would not thrive in beds and the yield would be affected reducing the cost benefits of pots in the since due to yield losses. All the Blueberries plants are drip-fed water and nutrients (Urea, Calcium & Nitrate) through pipes that run through the beds. Tesco is the main market for the blueberries produced here, with about 80% of the total produce going to the Tesco market, with the rest going to M&S and wholesale markets. Most of the produce is transported to the UK, it takes approximately 40 days from the blueberries being harvested, until they are on the shelfs in the UK, and Tesco’s will pay the farms 90 days after the fruit has left the farm, making it easy for farmers to budget and giving blueberries farms a reasonably reliable and consistent cashflow throughout the harvesting period. The harvesting period usually begins about April and lasts through until October, meaning harvest is approximately 5 months long, and during the peak of harvest between the Pinfeilds farm and the packing house the blueberries are transported to be processed at Hidden Valley farm, the business employees approximately 500 staff, so it is a very labour-Intensive business. As well as being a labour-intensive business, the blueberries production is also very water intensive, Pinfeilds need approximately 1,500,000 litters of water a day to irrigate the plants in the peak of their season, this water was initially taken Nora valley (11k away) but due to the expansion of the farm, they were unable to meet their water requirement, so in 2020 Pinfeilds put in a new pipeline into the Chinyika valley (14k away). This pipeline can produce 220 m3 of water an hour all year rounds, which means not only are pinfields meeting the water needs, but they also can expand in the future.
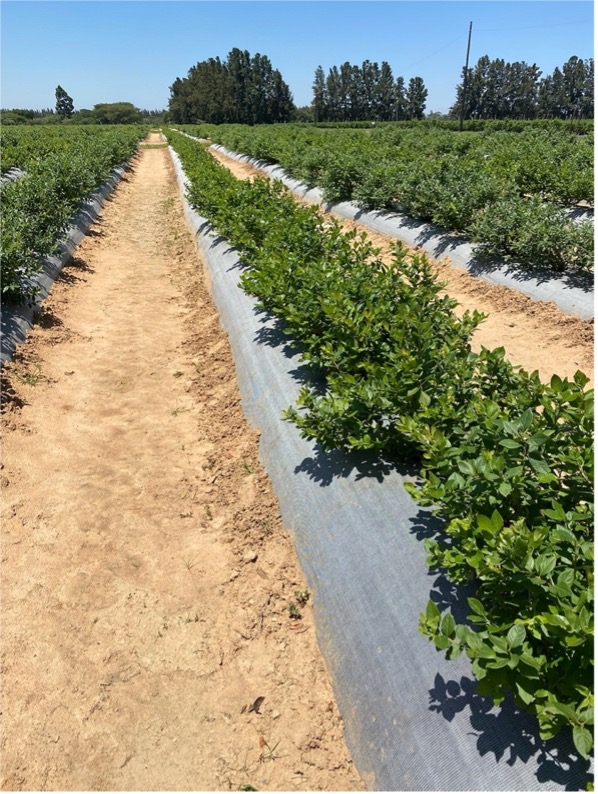
Figure 1. shows one of the different verity’s in-between the 2 beds of main crop beds, as you can see the main bed photographed in this picture is a lusher colour of green, this is because it is a different verity from the main plants.
This is a different verity as it is used to help with cross planation, every 3rd bed is a pollinators bed, this means that the yield on these beds is not as good as the main beds however, the benefits to cross pollination they provide creates a better fruit set on all the plans, and also increases the sizes of berries that are on the plants.
There are beehives that are brought in by contractors and they are placed around all fields to make sure that all the plants are going to be pollinated.
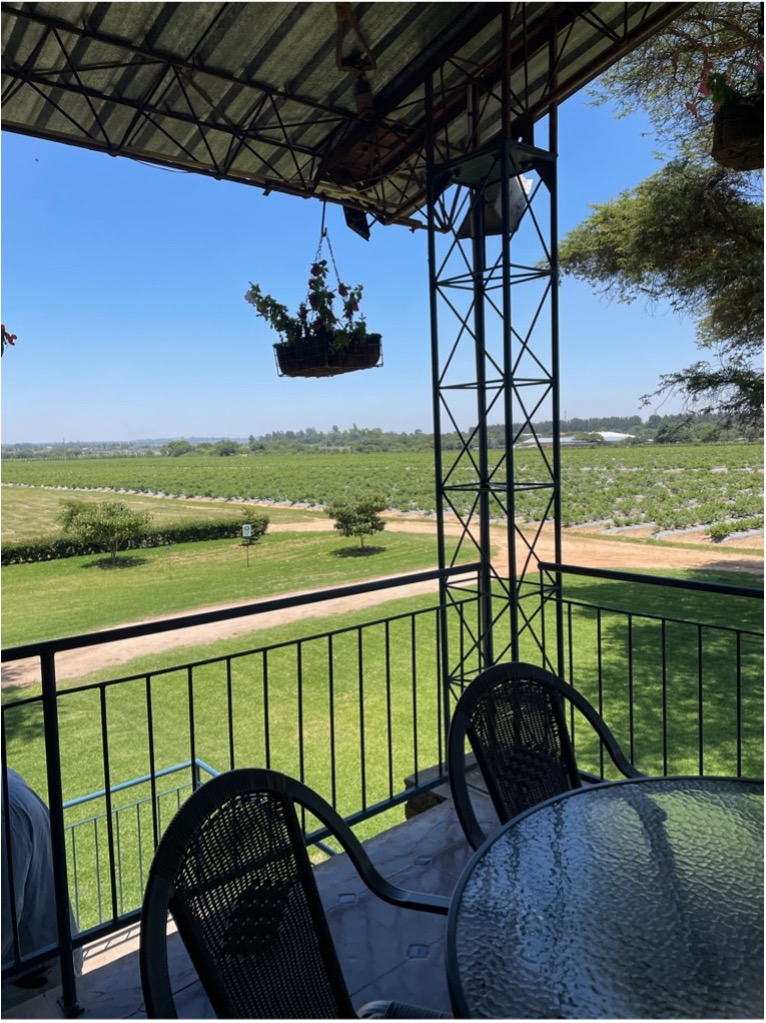
View From Office at Pinfeilds Farm
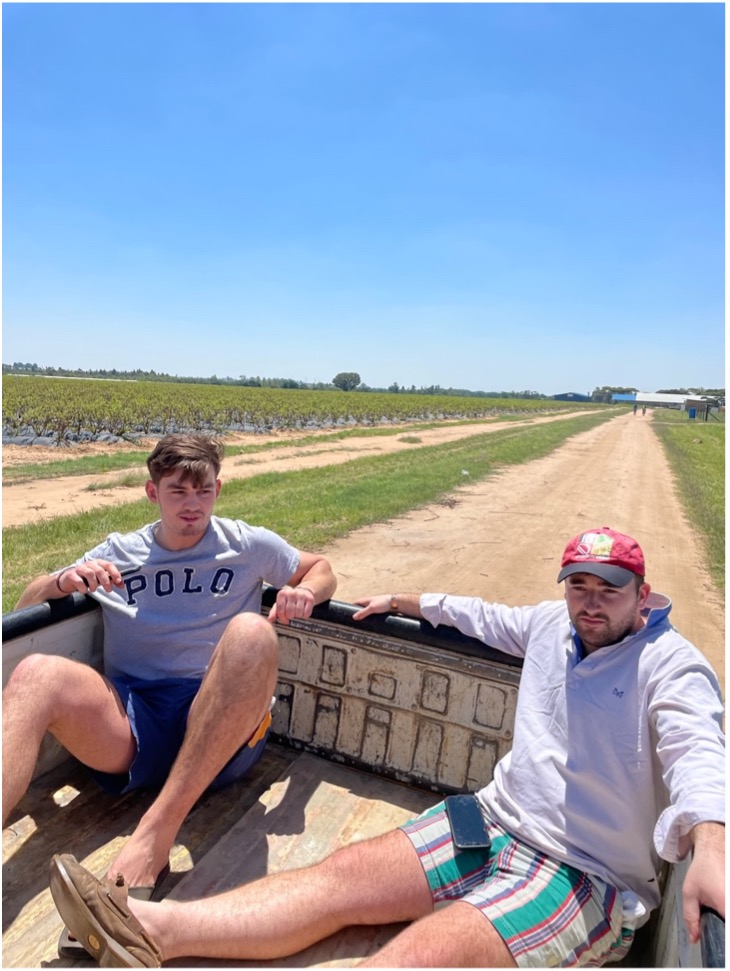
Driving through Pinfeilds farm
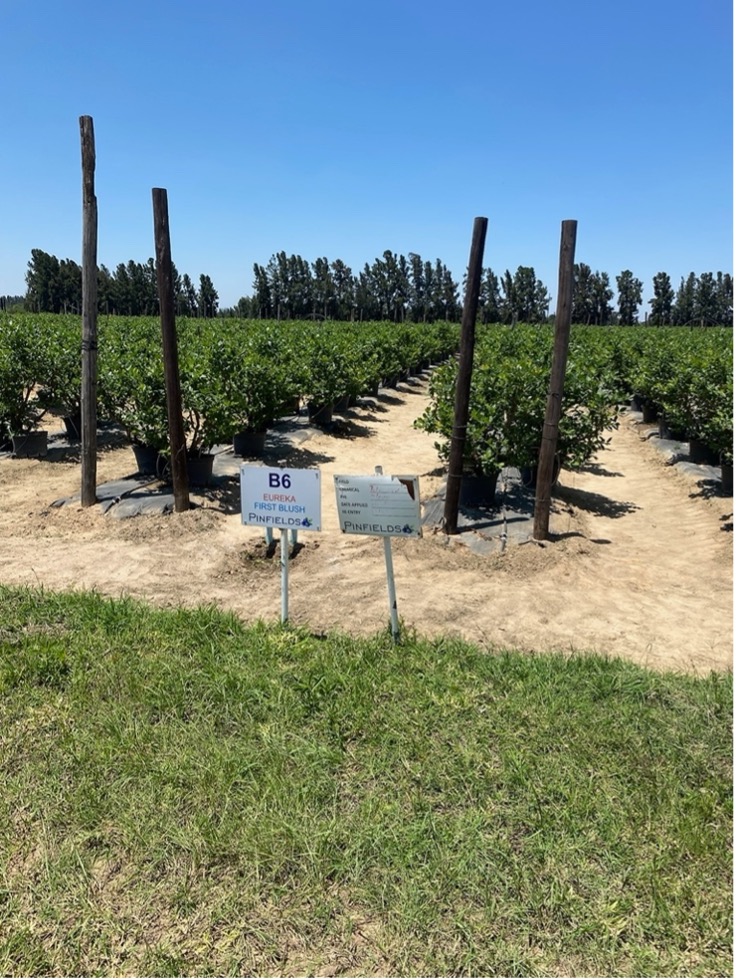
Trial plots on the farm
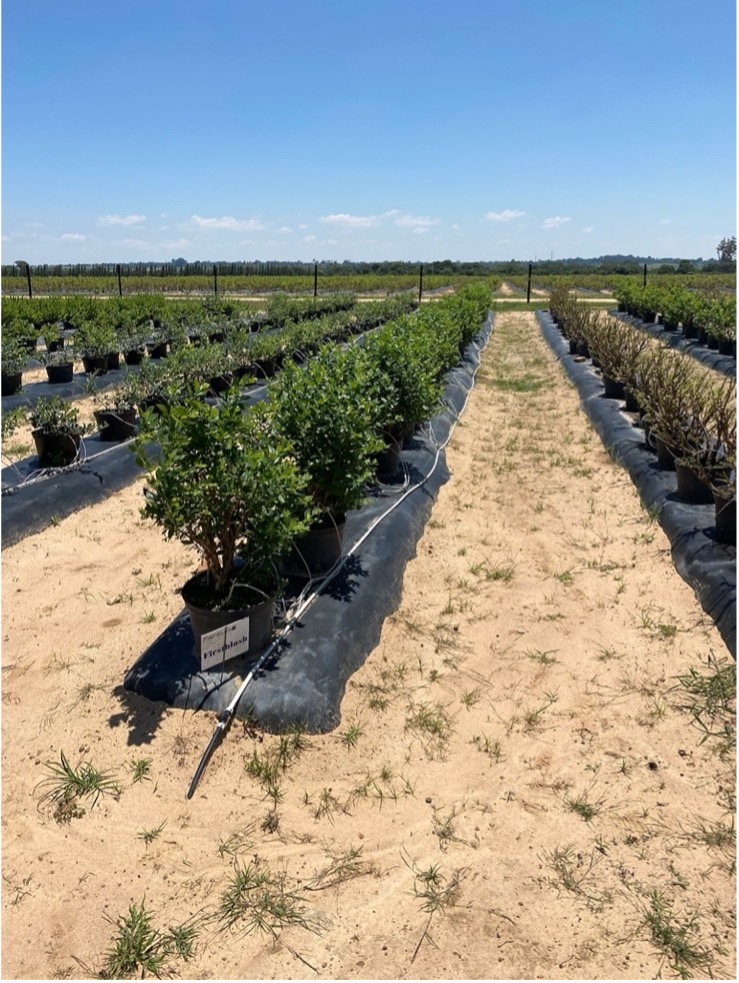
Some more trial plots
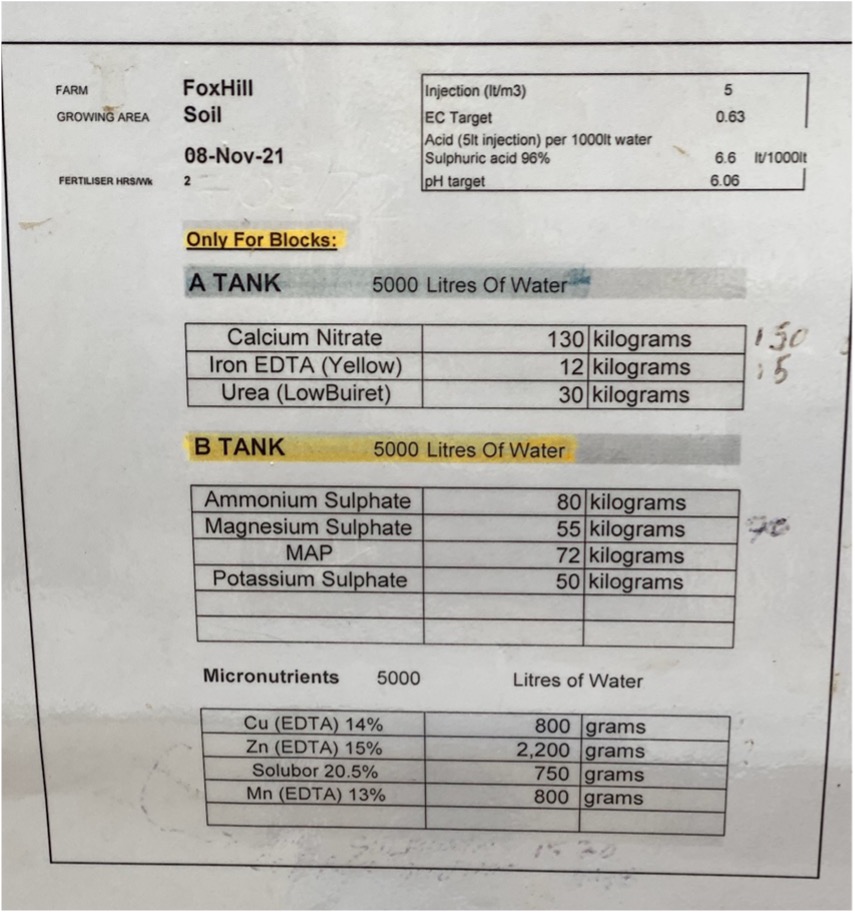
Figure 7. is a picture of Foxhills fertigation plan, although this is from Foxhill farm, it is fairly generic plan and a very similar to the plan used at Pinfeilds farm, all the chemicals in this plan are sent out to the plants through the drip irrigation systems. Figure 8. below is a picture of the farms chemical store, chemicals are administered and mixed in these big tanks before being sent out around the farm through the drip irrigation systems.
Although we went out with the harvesting period of the blueberries plants it was still very interesting seeing how productive these blueberries farms were, and how much imputes goes into the production systems.
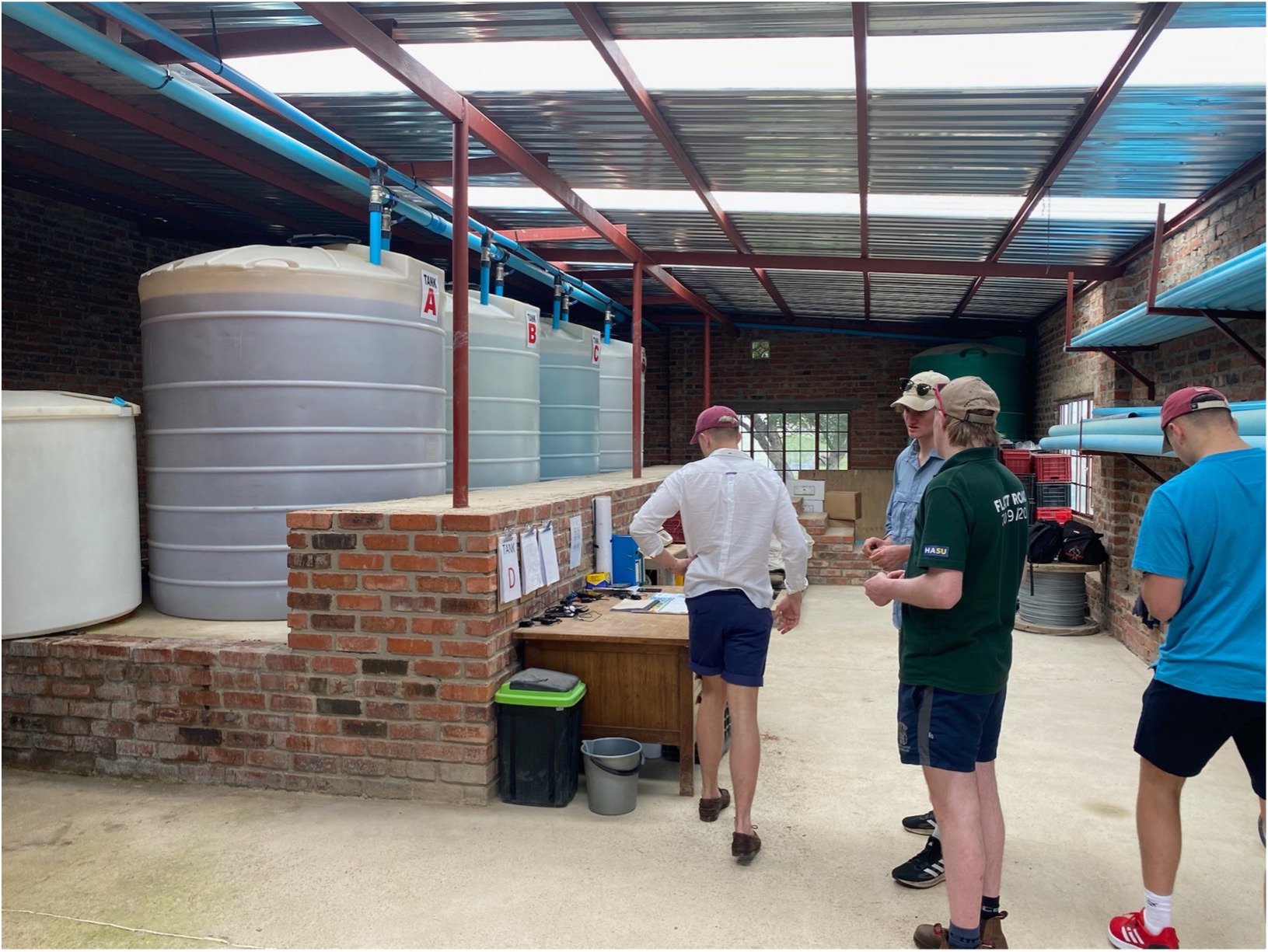
Chemical/fertiliser store and pumping station
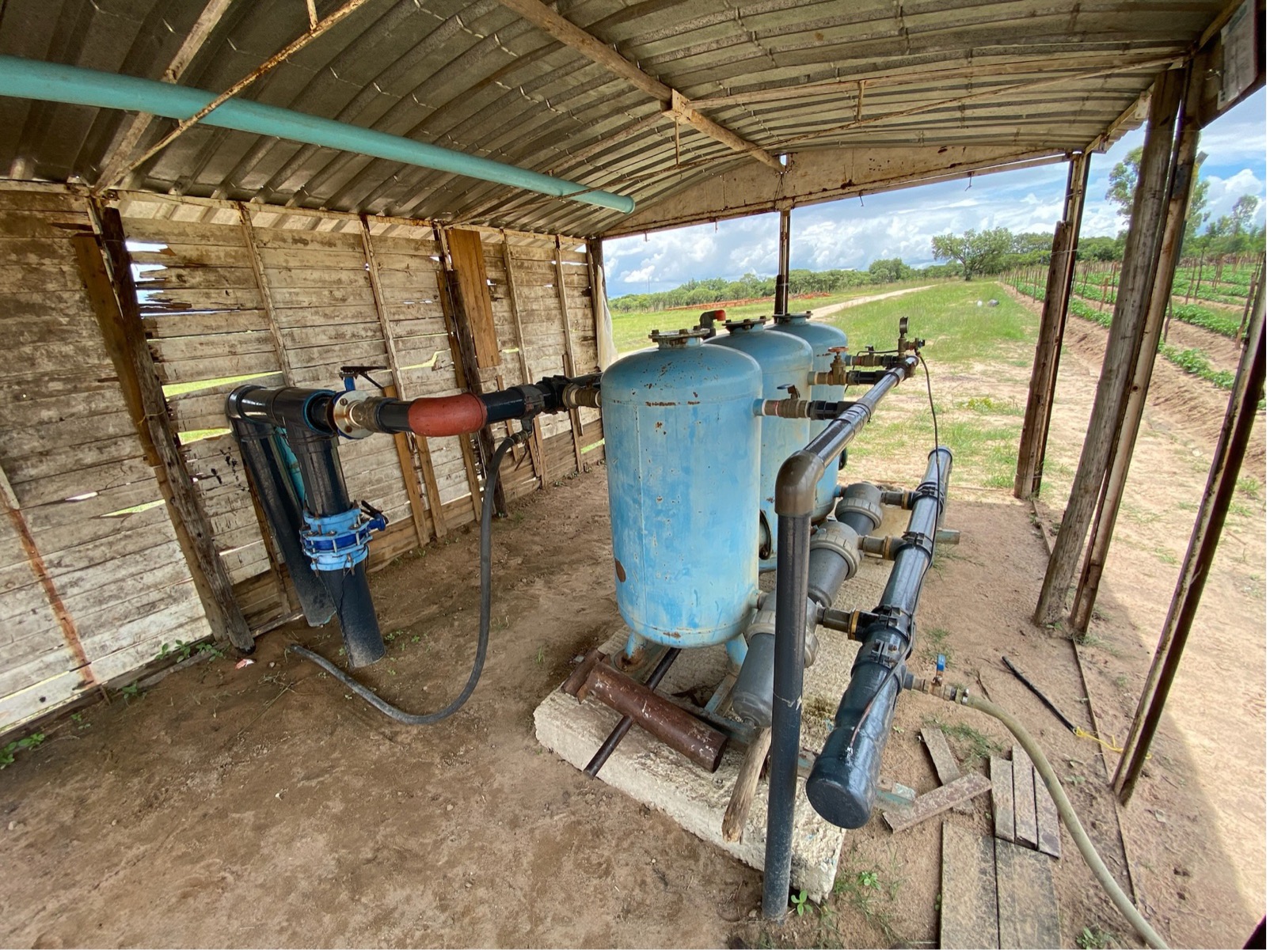
Water filtration system
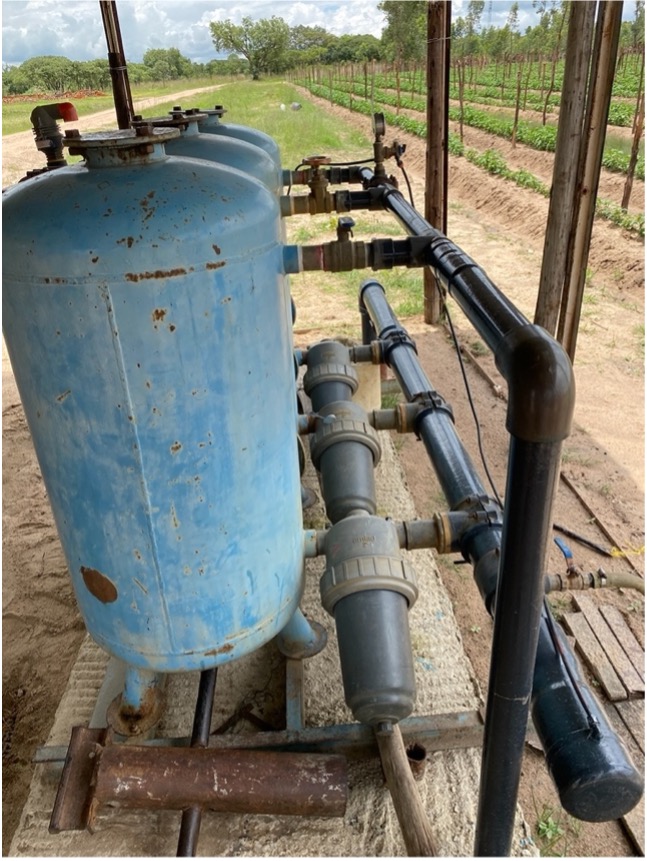
The water filtration system that is used on the farm, all the water comes through these tanks, and the tanks are filled with sand, which acts as a filter, taking all the algi and any dirt that might be in the water out of it, it is from here pumped up to the chemical/fertiliser store before being mixed with the chemicals and fertilisers above.
The blueberry plants on the farm are kept for 7 years, year 1 there will not be any crop, just pruning the lower branches to get as many bearing points as possible.
Each worker can harvest approximately 50kg of blueberries a per day, and about 80% of the workers are females, more of the managers are male, however the women seem to do a better job at picking the fruit, don’t talk and argue as much an have better attention to detail so we were told on our tour which was very interesting.
Each plant will on average yield approximately 3.5kg of fruit over the entire picking season. Once the berries have been picked, they need to get to the pack house as soon as possible to maximise the shelf life of them, every hour they are sat in the sunlight will reduce the shelf life of the berries by an entire day.
The berries are aimed to between 12-16mm, and they averaged a price of $3.5/kg last year in 2022 which has been the worst year due to many factors such as strikes in South Africa as well as South American fruit coming into season earlier than normal.
Normally the average price over a season will be over $4.50 a kg but can be over $5.00 a kg if quality and timing is good. Last year the business struggled slightly more than most years, 80% of the produce is transported to the EU via ship, however due to these strikes in the South African ports last year, there was a lot of late shipments made into the EU. Due to the fruit being delivered late to Europe they coincided with south American fruit so the market was flooded the market and overall price for fruit was reduced massively.
Pinfeilds Pack House
The pack house at Pinfeilds farm can grade and pack approximately 14 tonnes of blueberries per day, this means it has sufficient output to process all the blueberries produced on the farm but running quite close to maximum capacity.
Over the season approximately 800 tonnes of blueberries go through the packhouse. Pinfeilds has recently put in a flow berry sizier costing $150,000, however this payed for itself within the first 4 weeks of grading, very good return on investment. Over 14 tonnes of produce per day there is only 2kg of rejects per day, even at the peak of the season. The largest cost for this business is the cost of transport.
Unfortunately, while we were out here, we were out at the wrong time of the year to see picking and the pack houses operating, however I will try and attach some videos we have been given from Kelly as an attachment, so you are able to see the pack house and the new grader they have installed, in action.
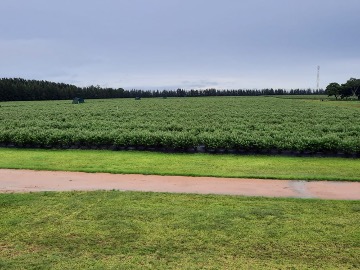
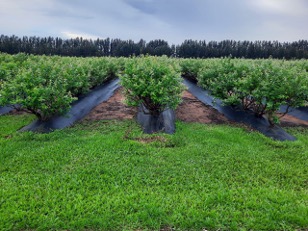
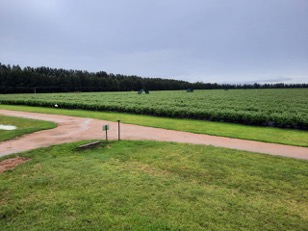
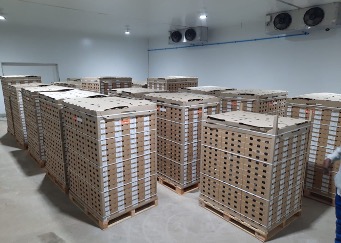
Hukuru Quality Day Old Chicks
Hurkuru day old chicks are located on the Moore-Gordons farm, Hurkuru have controlled the rearing/breeding flocks as well as the hatching process.
Being able to control all the aspects of the process form breeder flock placement to hatching of the day-old chicks allows Hurkuru to process the best quality chicks as it allows them to have much more control of the process.
Hurkuru are the second biggest producer of day-old chicks in Zimbabwe, hatching around 500,000 a week depending on orders. This contributes to 40% of day olds hatched in Zimbabwe.
Hukuru use Aviagen’s Ross 308 which is one of the top broiler chicken breeds used in the world. The Ross 308 has very good meat yields, good growth rates and feed efficiency, as well as having high egg production number which means that the Hukuru will have to replace their parent flocks less which have an incredibly high cost on the hatchery.
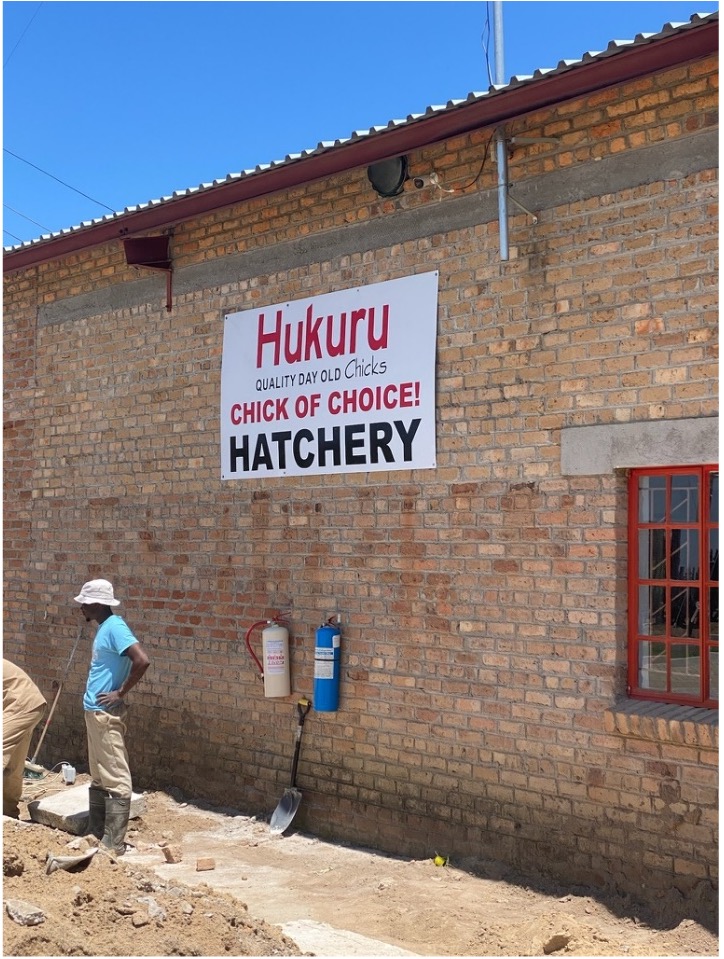
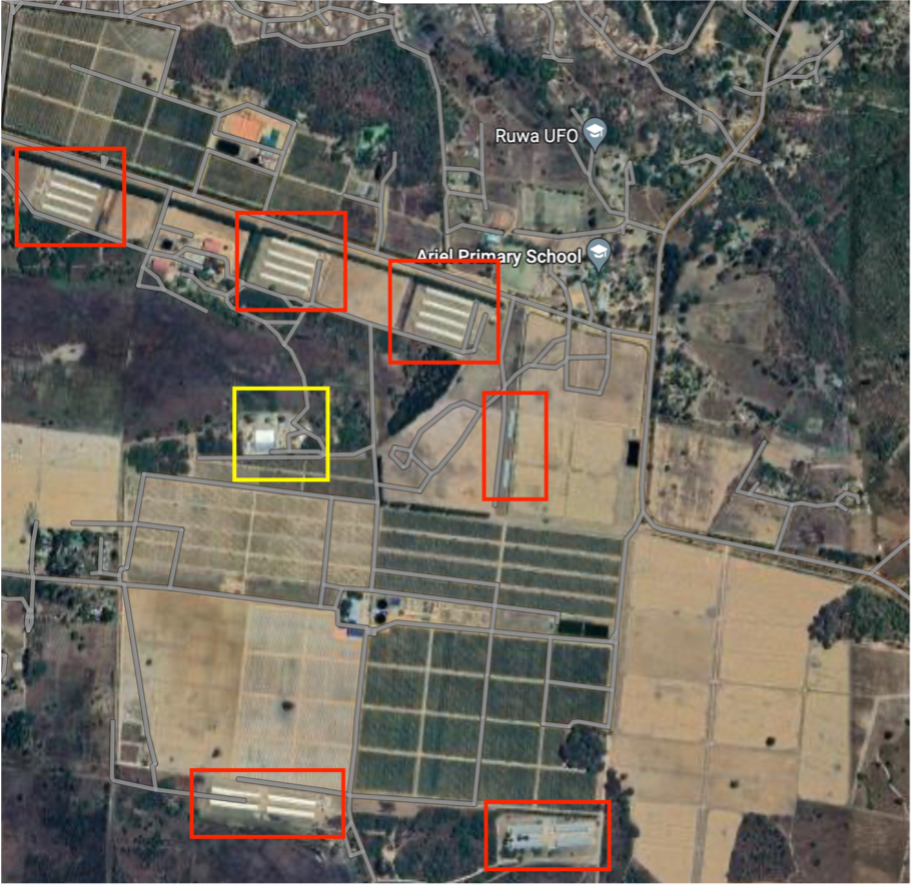
In the picture to the left, it shows the site at Hukuru, the chicken houses are identified by the red outlined building, each separate site is responsible for the brooding, rearing and breeding of the flock for the entirety of their life.
Hukuru have a verity of ages of breeding flocks present on their sites at one time, this allows them to always have the right number of eggs supplied to the hatchery at one time. Each site has the same number of chicks placed on each site, 22,000 pullets and 3,300 males.
On placement day the chicks are flown in from Zambia into a local air strip where they are them placed in the chicken houses on site, the parent flocks for all chicks placed in Hukuru come for Aviagen Central Africa in Zambia.
Brooding/chick placement is one of the most important aspects in growing both broiler and breeder flocks for Ross 308, it is very important that feed, water and temperature are correct otherwise the development of the chicks can be affected and resulting in poor crop performance such as bad gut health that will affect the crop throughout its life.
The house is heated for the first week, the house air temperature at placement is ideally 33 degrees and as the chicks get older temperature is decreased until maturity.
After four weeks the rearing process begins, this is where the birds are graded into different weight category’s so that different feeding programs can be introduced so that the birds all come into laying at the correct age.
At 24 weeks of age the flock should start to commence laying, when laying starts males and females are feed different ratios, this is to promote different behaviours and conditions to suit what is needed form the different sex.
This is achieved though different feeder heights. The flock goes through different percentages of fertilization throughout the ages of 24 and 64, peak fertilization occurs around weeks 35 – 37.
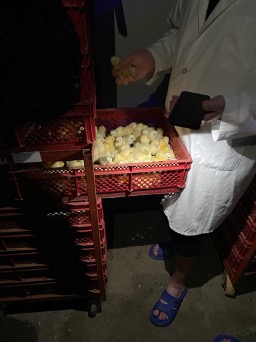
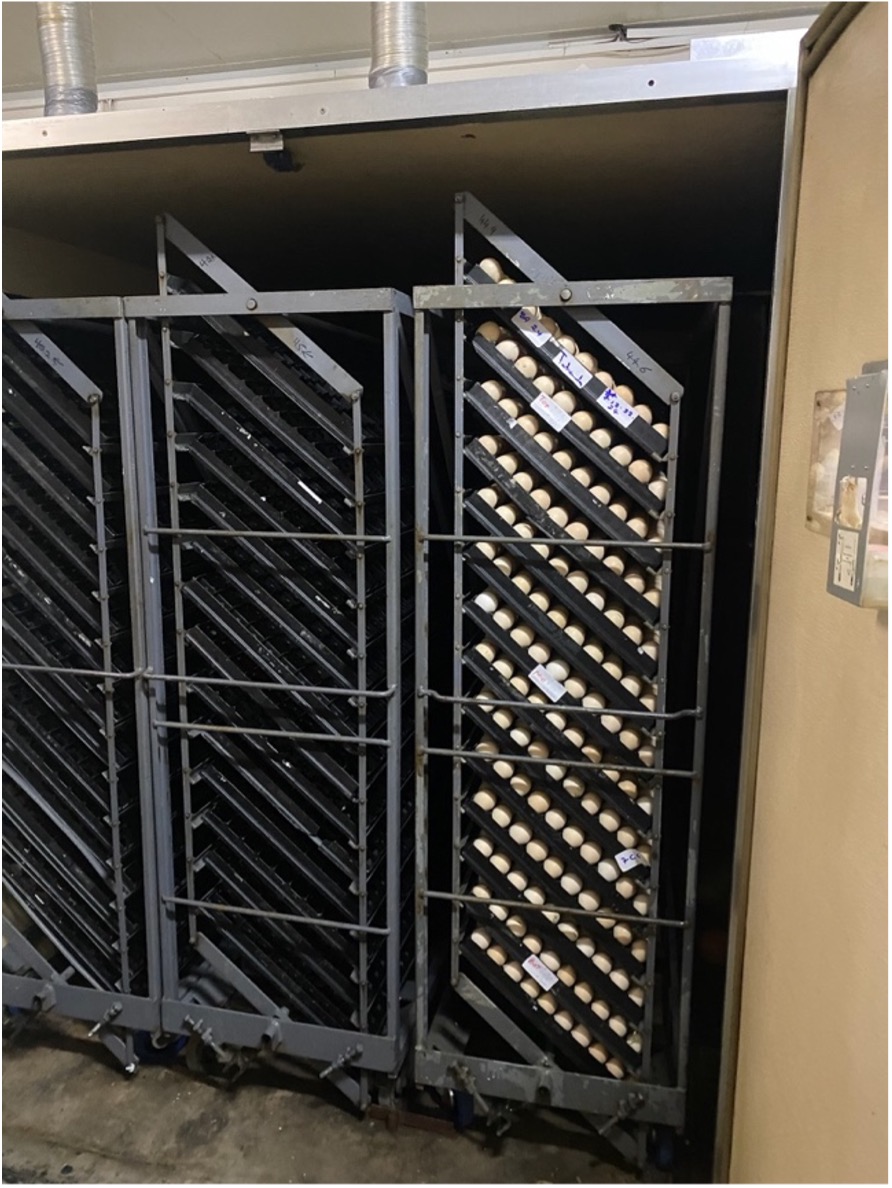
Once the eggs are brought into the hatchery, they are stored at 18 degrees for up to 10 days until they are graded and transferred to setter trays.
This process is where the eggs are turned 45 degrees, this simulates the natural movement that a mother would move eggs while brooding on top of them.
There are 16 trolleys in each setter which is a capacity of 89,444 eggs. The eggs are in the setters for 444 hours where the temperature, humidity, CO2 and ventilation are controlled carefully; the eggs are turned every hour.
This is all controlled form a smart centre control system. After 444 hours of being in the setters the eggs are them moved to the hatchers.
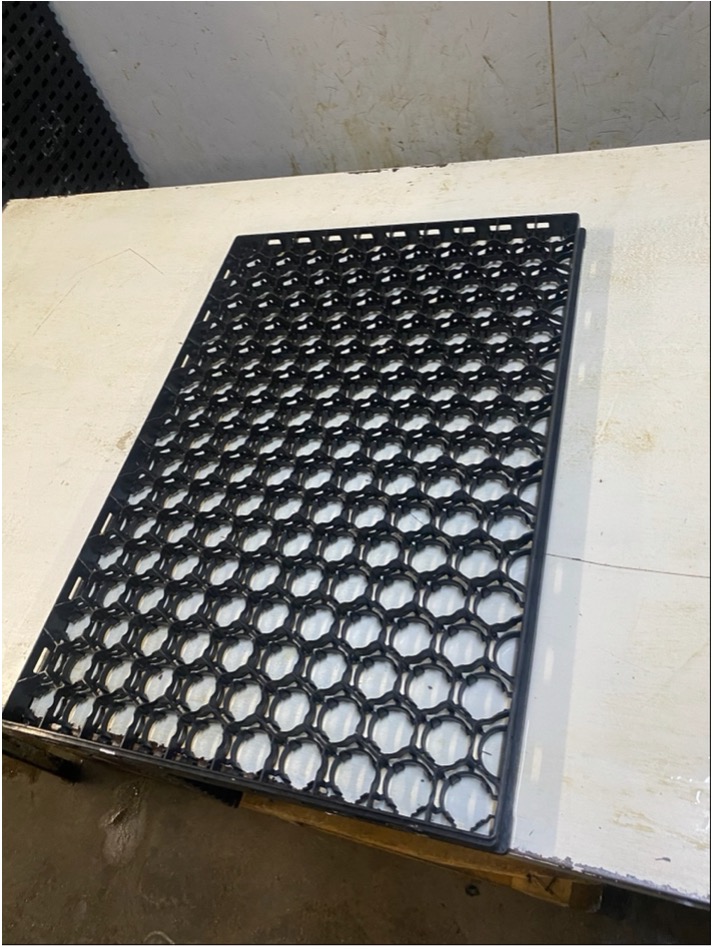
Setter trays, for storing eggs in trolleys
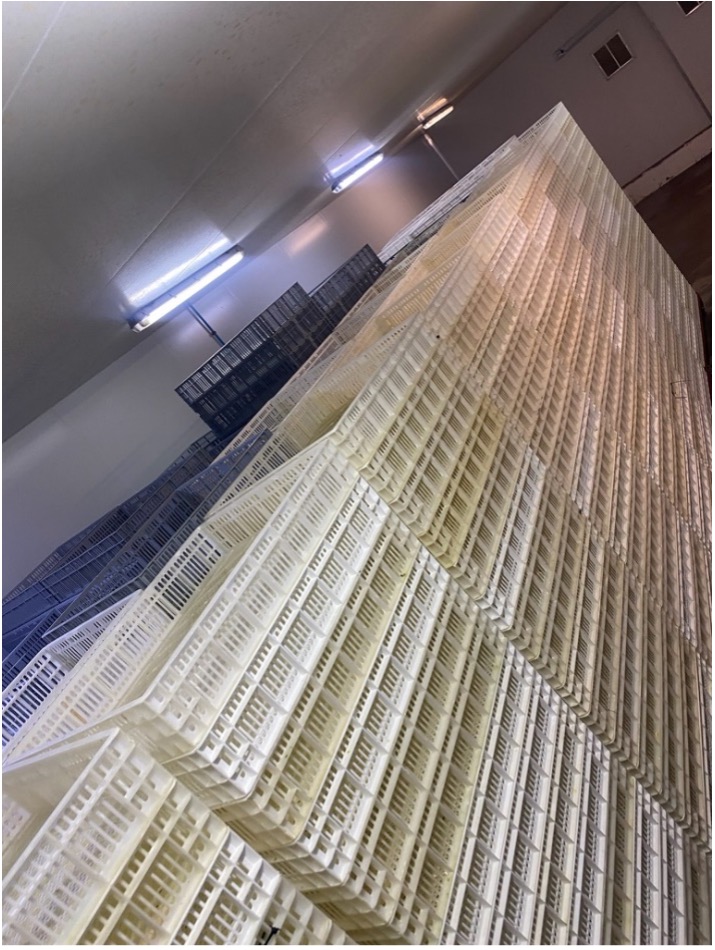
Hatching trays ready for eggs to be transferred into setter
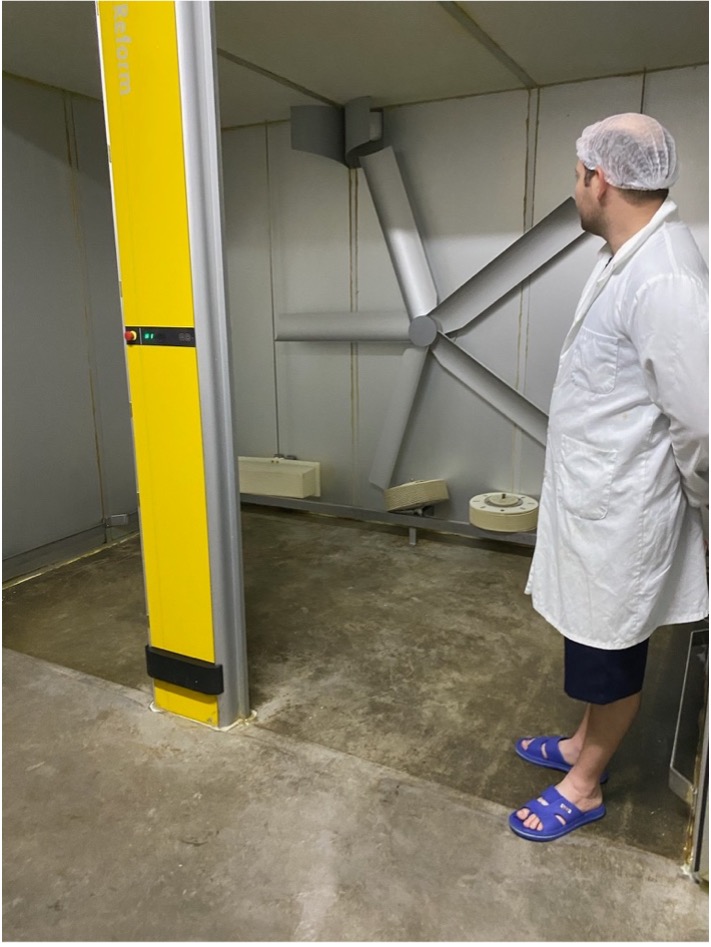
Empty Hatcher
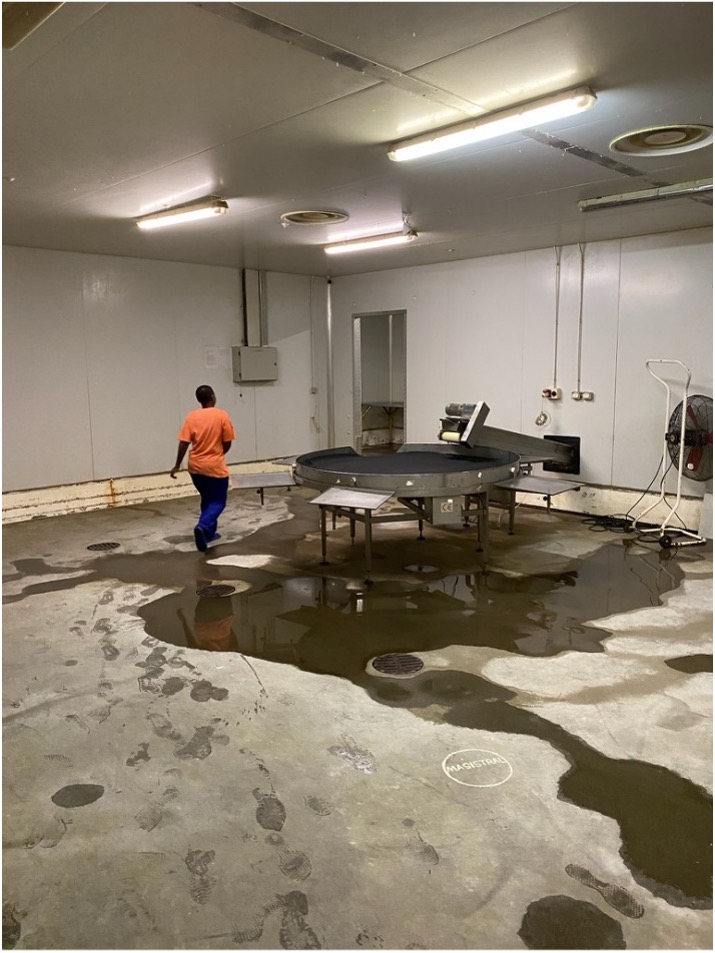
Chick grading and counting table
Once the eggs have been transferred from the setter trays to the hatching trays after 444 hours in the setters, they are transferred to the hatchers. The hatchers are also controlled very carefully for temperature, humidity, CO2 and ventilation; this is very important as if the hatchers are too hot when the chicks are hatched, or ventilation isn’t good enough this will affect the chick’s development early or even lead to chicks dying in the hatchers before chicks are removed.
Once the chicks are removed from the hatchers, they will be first graded out the trays, this grading to remove deformities and culls such as yock sacks still attached. Yock sack is a common cause of early death within chicks, these chicks need to be removed in order to prevent the spread of the bacteria spreading.
When the chicks are moved onto the counting table a secondary grading takes place as a double check that no poor chicks are a delivered to farm as well as the hatching count. All chicks have a spray vaccination applied and some orders have an injection vaccination applied, these vaccinations are to be aimed to promote gut health which is vital for broiler production as this keeps the good feed conversion ratio and growth rates.
There are different mixtures and combinations of vaccinations applied to the birds this depends on customers options and what they are willing to pay.
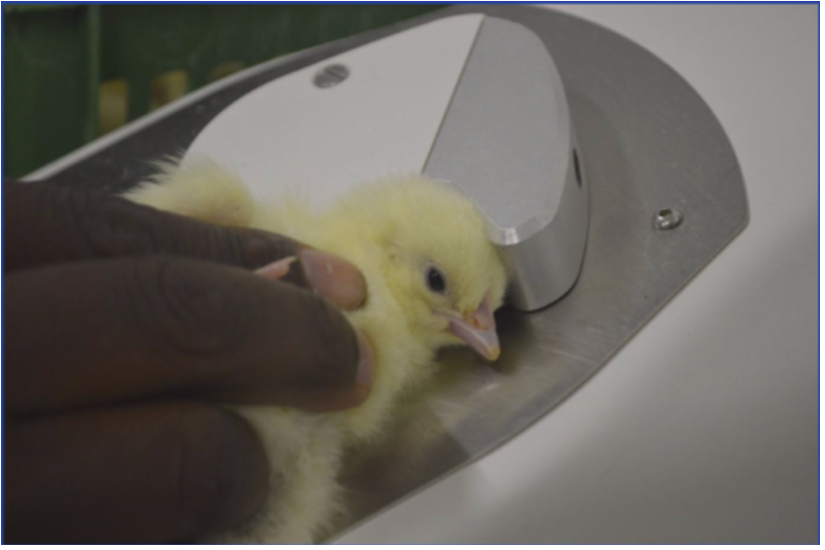
Currently chicks are 70 cent per chick to buy form the hatchery however in peak chicks have costed 90 cent per chick.
Hurkuru have a minimum order of 5,000-day old chicks, however many Hurkuru chicks will end up on small holding around Ruwa and Harare.
This is due to secondary agents who run distribution companies in chicks. These chicks passing form hand to hand being distributed in townships in the nearby area, these chicks can be sold five times over and can reach a price of 5 dollars per chick.
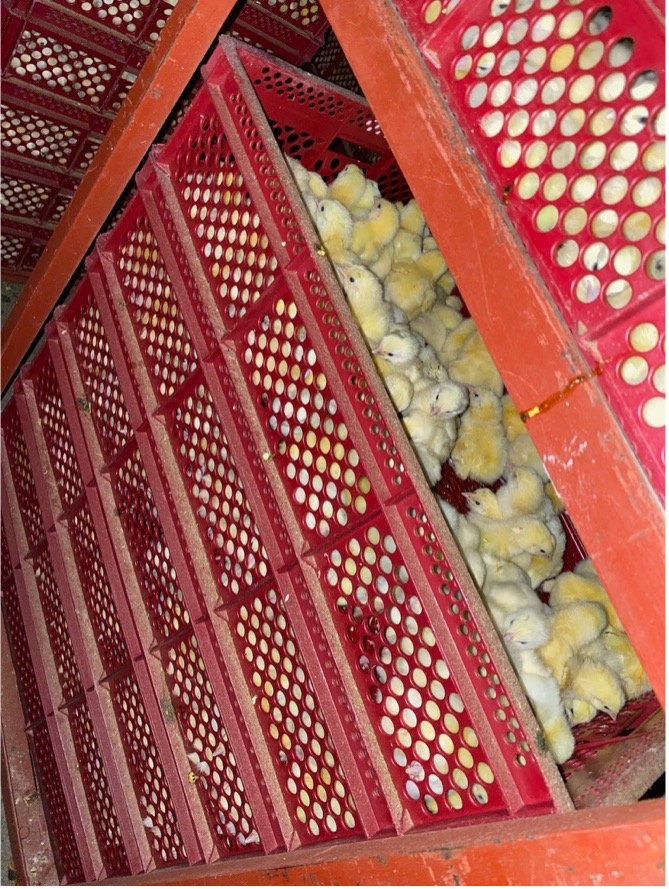
Cherry pepper production within Zimbabwe.
Over the period of the trip, we were lucky enough to visit two farming businesses which are part of the major growing co-operative for the Zimbabwean cherry pepper production.
Our first farm was managed by Marcus Philp who is an ex-Harper Adams student who finished his studies in 2020 with an engineering degree. Our group travelled round their farm which is known as Foxhill and is located around 45 minutes from the capital Harare.
This set-up is situated within a ring fence and has been farmed by them for the last 2 years. Initial investment extended to new irrigation systems, for both blueberries and cherry peppers grown on the same site. A new farmhouse has been built as well as on site accommodation for members of staff.
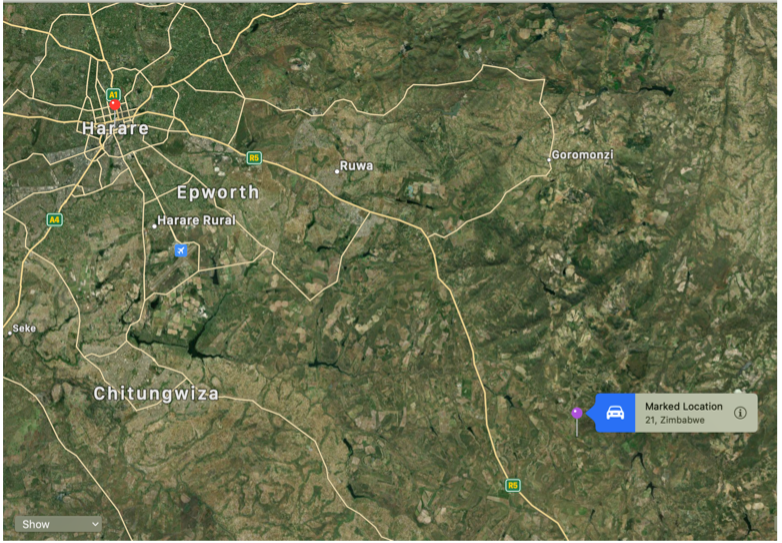
With cherry peppers being ideally suited to rich soil the bottom of the farm sees a higher level of production. The soil can be described as a red clay loam which is due to lower proportion of clay is free draining. The growing process begins with raised beds being cultivated with disc ploughs.
These are formed either with a gap the width of bed every third, this is to allow the air assisted sprayer to pass down the beds without causing damage to the plants. Alternatively, all beds are planted when spot sprayer takes place by hand.
Air assisted spraying seems to be the quicker option and requires a smaller labour supply but can does not show the same accuracy and has the potential to waste chemical.
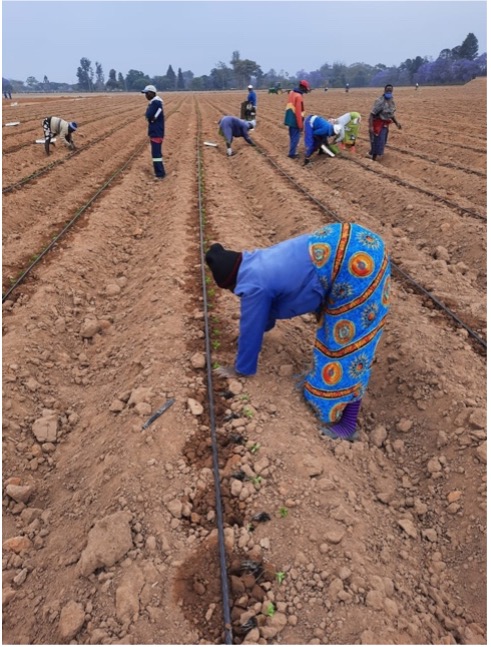
Transplanting cherry pepper plants
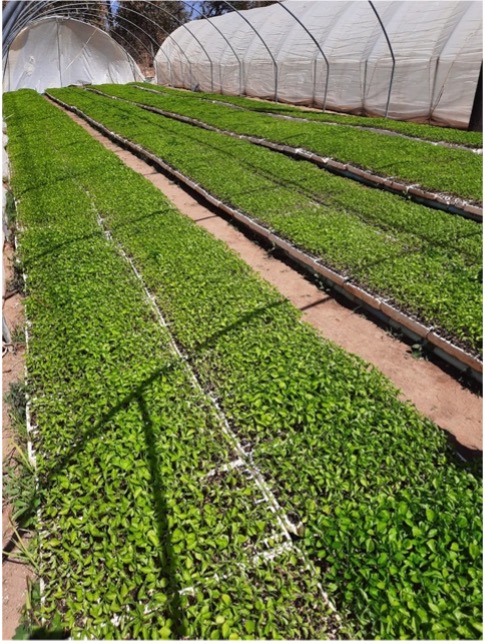
Trays containing cherry pepper seedlings
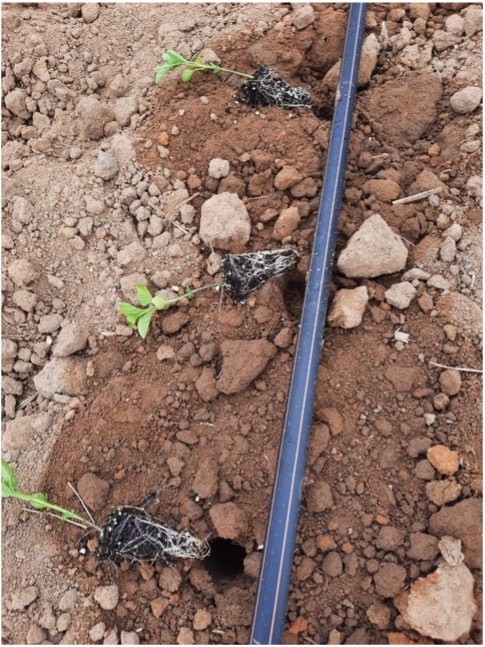
Seedling ready to be planted
The planting process can be seen from figures 27, 28 and 29 showing the how the seedlings are grown under poly tunnel conditions for part of the year. Hidden Valley agriculture have a very established plant nursery which in years prior have grown a large proportion for the group. This year on the other hand both farms grew their own seedling in house.
The holes are bored by hand then fertiliser is placed into hole before seedling is planted. This is to give initial boost for seedling instantly. These bed widths are also dependent on the quality of the soil, poorer soil will force plants to be further away as they colour with the sun which will have more chance to get in with wider gaps.
The drip-fed irrigation system is re-laid ever year as it is an annual crop, this is done before the crop starts to put on green bulk to make the process easier. With planting taking place then the posts and wire are put in place to encourage upward growth of the plants.
Without this structural assistance being put in place lateral growth would occur making the management of them farm more difficult. The bushes become heavy once full of fruit.
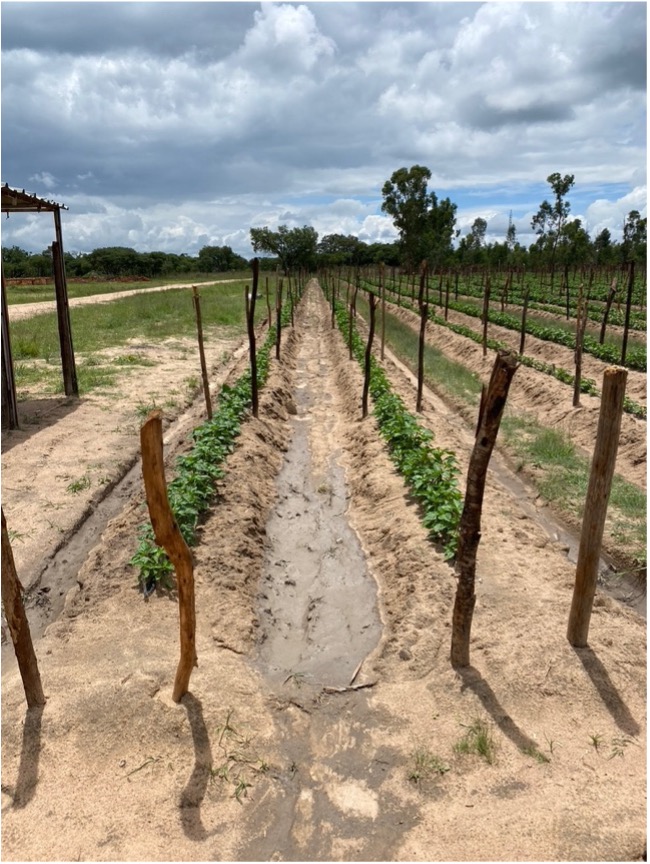
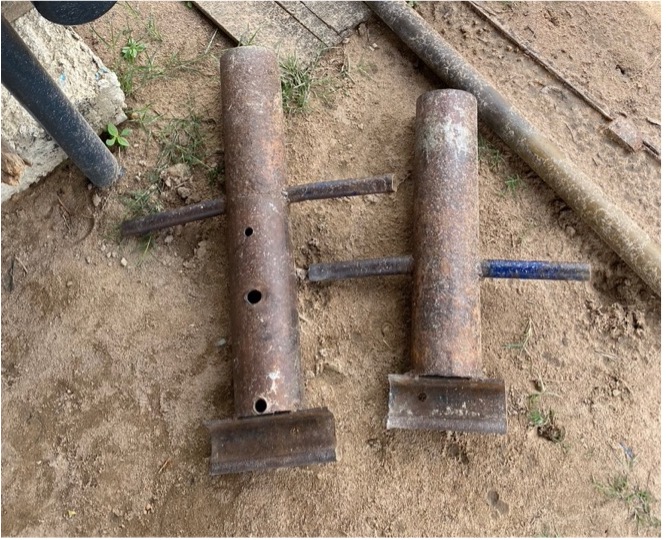
Posts being put in place, this is all done by hand with post knockers.
This for reference takes 10 days to put stakes up and a further 2 days to string up a 7.2 horticultural hectare block. In their system these are the timing but would take less time if there was more labour available.
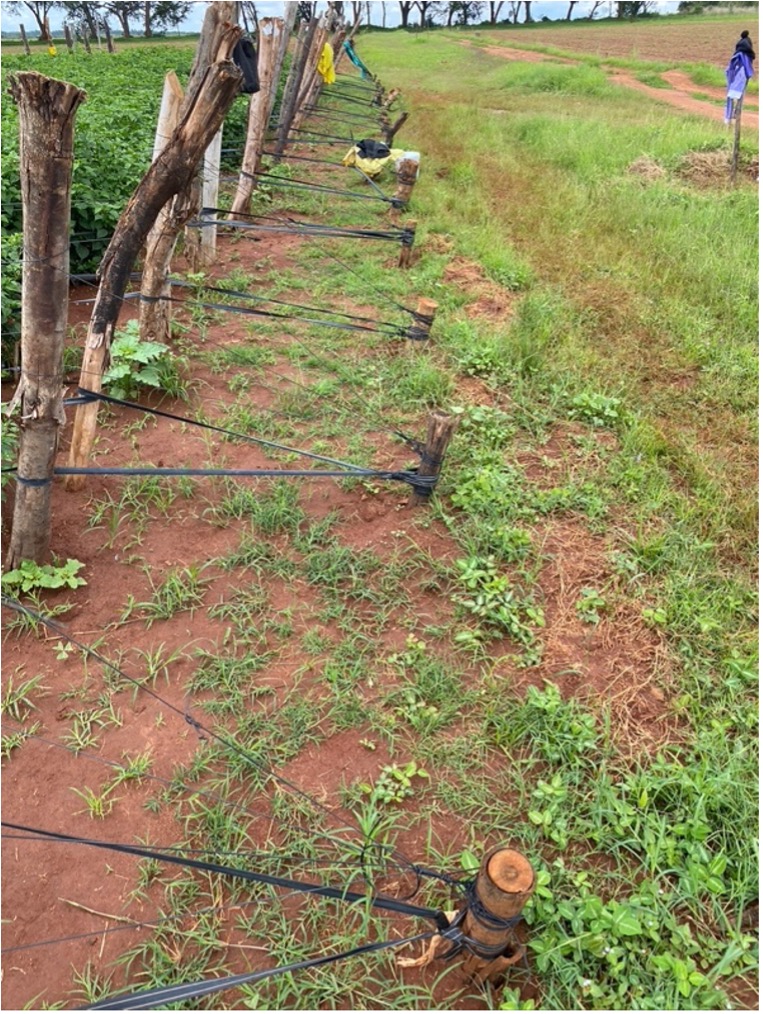
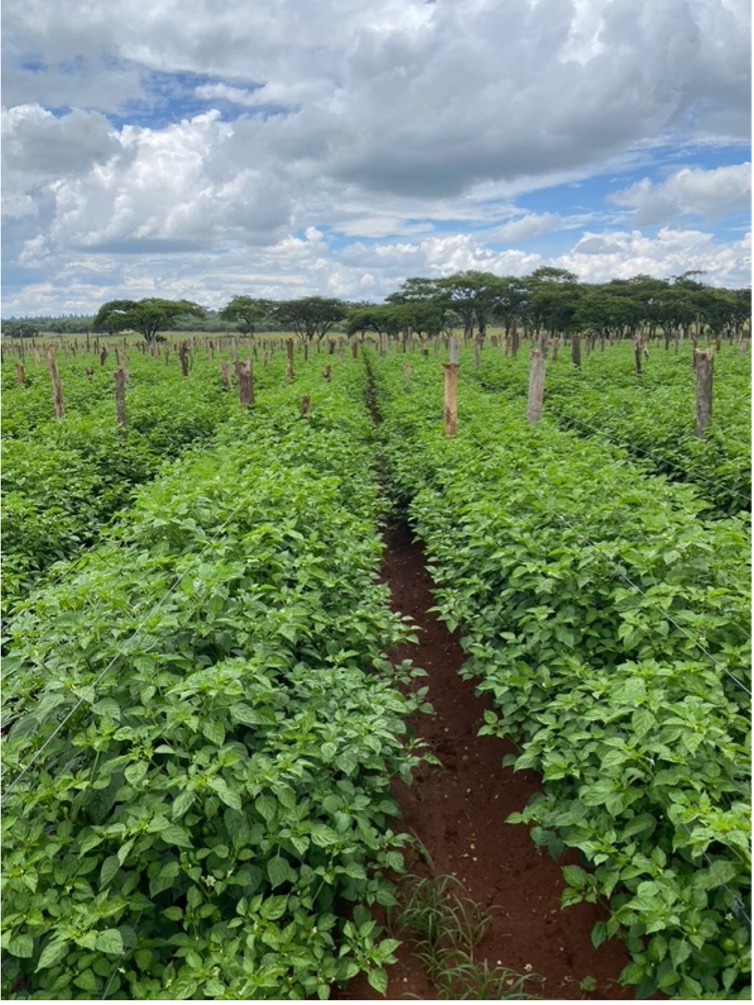
At the time of visiting Foxhill Farm there was 2 different stages of crop which were grown on slightly different soil types.
One crop was grown on the red soil and can be seen pictured in figure 8, which was planted in the last week of August. These were seen to have very well-developed canopies with a lot of green fruit.
The other crop was transplanted into a courser sandy loam which is well drained to suit the production. Unfortunately, as pictured in figure 36 there was significant residual pre planting herbicide, this can be seen with very patching establishment.
The remaining plants should establish given time and consistent water supply, with added nutrient supply. The water system on these plots is derived from both an existing and new reservoir.
As previously mentioned, the water is filtered through initially a larger tank filter which is filled with sand then a small disc filter. This is very simply technology and has been in place for many years prior but is effective in removing the algae and dirt from the water supply thus allowing the drip irrigation to flow freely without blockage.
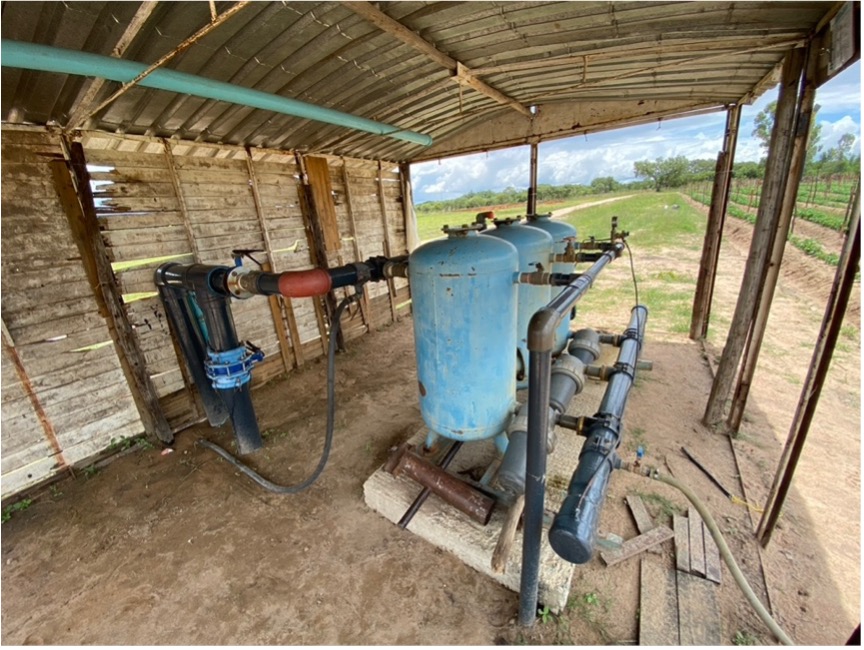
At this same site there is a very new system which was put in place shortly after the Philp’s took over. This was more irrigation equipment which is powered by 30 panels. This solar system also powers the farmhouse as well as the onsite packhouse. With Zimbabwe having a rather inconsistent power supply due to outdated national infrastructure, the solar panels remove the reliance on the country meaning all equipment works more seamlessly.
With the cherry pepper crop being grown in the warm humid climate there is requirement for chemical control of certain pests. The economically significant diseases include powdery and downy mildew alongside black spot which primarily attack the plant. As for insect pests these are Milly bug, Bole worm (see figure 34) which target the fruit and fruit fly which can be a vector for disease,
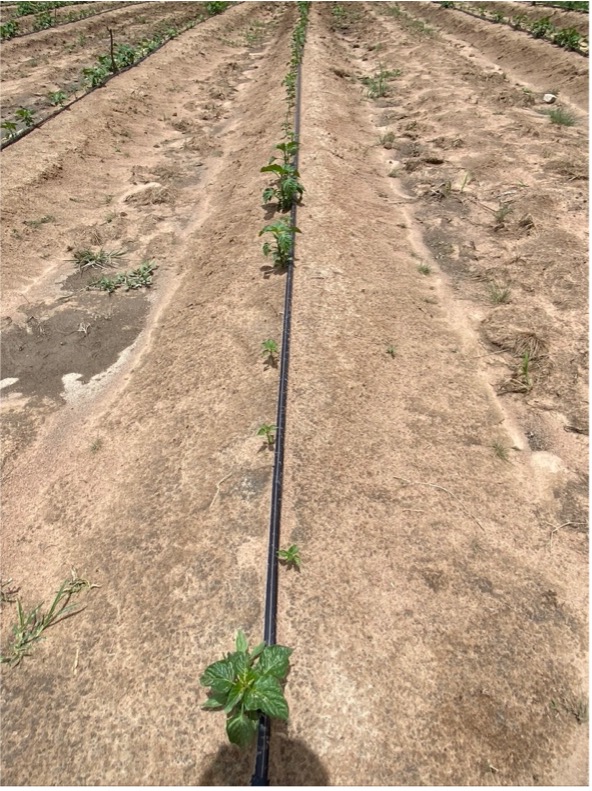
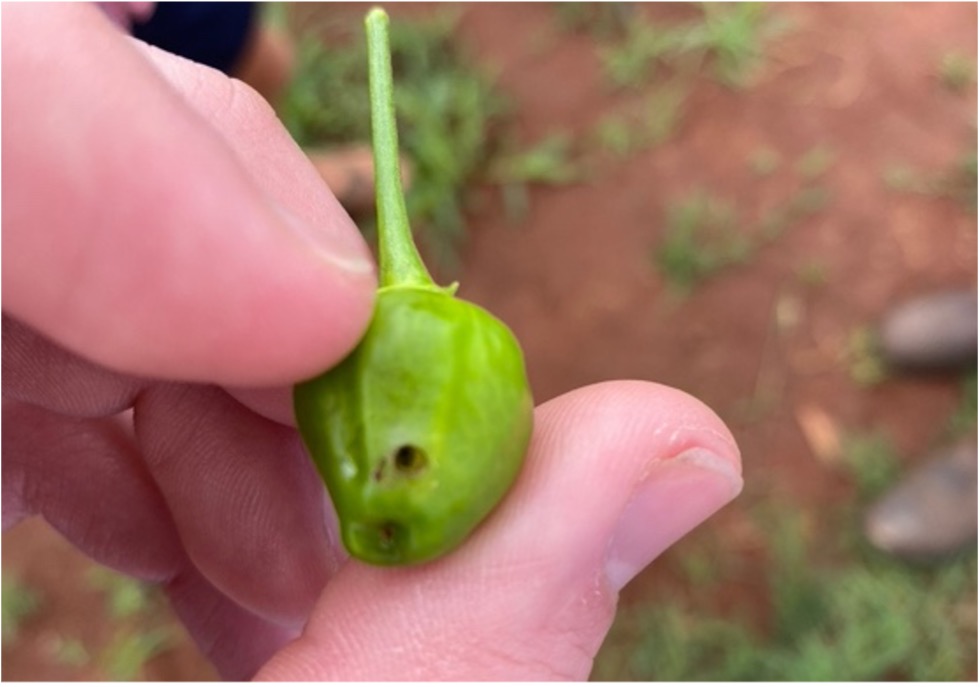
Fruit infested with Bole worm.
As mentioned before Hidden Valley agriculture is the other farming business that we visited and is where we spent most of our time. This farm is owned and farmed by Clive Moore-Gordon who is the father of Struan who attends Harper Adams with us.
They grow the same crops but just to a larger scale in the cherry pepper production with 18 ha being on site and 6 to an out grower, Tim Perrypeshco. By the end of our trip the cherry peppers were just about to start to be harvested.
Their projected start date does vary within due to the season but will aim to start between 10th and 20th of January.
It is a labour-intensive crop to harvest with 75 people picking and 215 in the packhouse alongside the 30 permanent staff. The pickers are massively efficient during the day being paid on a bonus scheme for increased output, they can harvest 200kg a day into 18kg trays.
In the packhouse they work at around 90% of fruit making it to packing. After grading the cherry peppers are graded, they are cored by hand then washed to remove any remaining seeds. This process should aim to achieve around 55% from fresh weight.
The company aims to yield:
- Early season yields of 37-43 t/ha
- Late season yields of 30-34 t/ha
- Early seasons pack out of 21+ t/ha
- Late seasons pack out of 16+ t/ha
There are 2 ways of export from companies named TNPC and Carara who require different specifications. These are that TNPC’s peppers are stored in brine containing preservative and Carara’s are exported with brine without preservative.
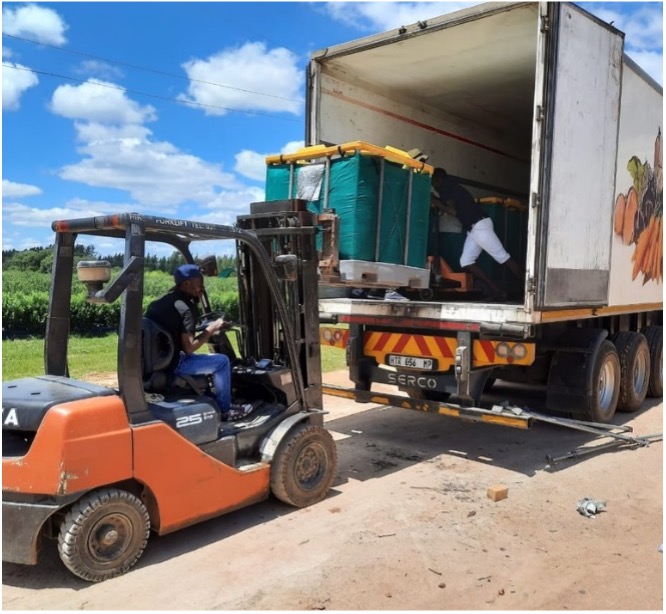
Price per kilo is as follows for Hidden Valley:
- Carara – €2.30 (making up 75% of the contract)
- TNPC – € 2.25 (making up 20% of contract)
- B Grade Fruit – €1.17 (Making up 5% of contract)
The premium price is paid due to the requirements being greater. As there is no preservative a whole shipment of 30 tons must be harvested, packed and transported on the same day. As only large producers can do this Hidden Valley takes care of this whole Carara contract.
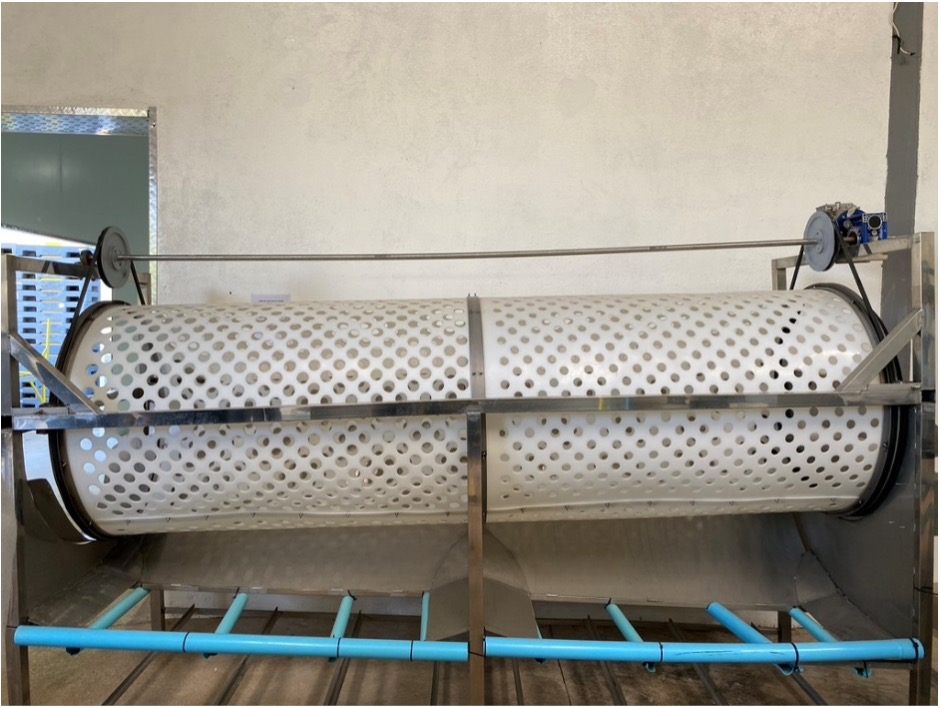
The size grader pictured on the left is used for sorting the cherry peppers by their circumference. Some producers lean towards wanting smaller cherry peppers.
This can be explained by them being stuffed with cheese for appetisers, cheese is the expensive part so smaller pepper requires less cheese to fill. The fruit can also be used for toppings and lower quality fruit can be used in sauces.
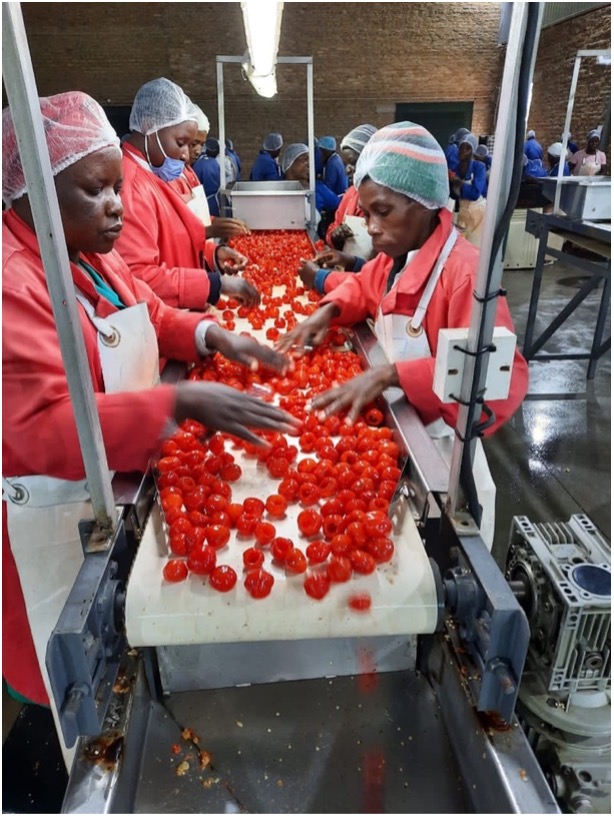
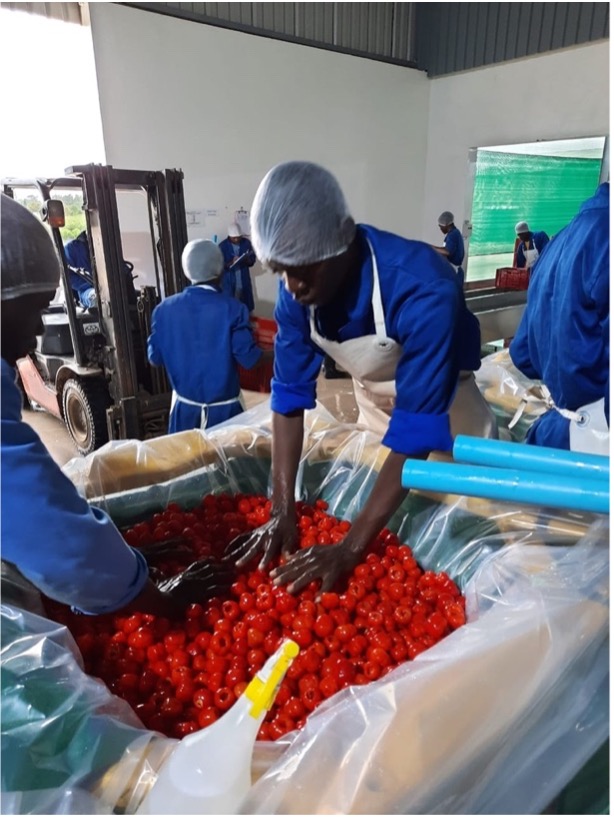
Within the cherry pepper rotation Hidden Valley use a cover crop. Unlike many farming systems there is no other cash crop included within the rotation purely cover crops.
It is a combination of Sunn Hemp which is a nitrogen fixing legume grown across Zimbabwe. This will reduce the requirement in future season for as great an application of inorganic nitrogen, reducing costs to the business. As seen in figure 40 there the nitrogen nodules can be found in the root system.
Another element of the cover crop is forest sorghum, which can be used to improve soil health by adding soil organic matter, enhancing microbial activities, and suppressing soil-borne pathogens in various cropping systems.
These cover crops go in for a year after first cherry pepper bushes have been desiccated and any surplus brash is burnt to reduce chance of disease spread.
Cover crop is then drilled then grows until desiccation for another cherry pepper crop to be drilled the next year. Depending on availability of land, cover crops could stay in for 2 growing seasons.
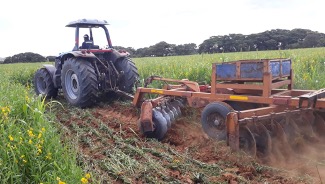
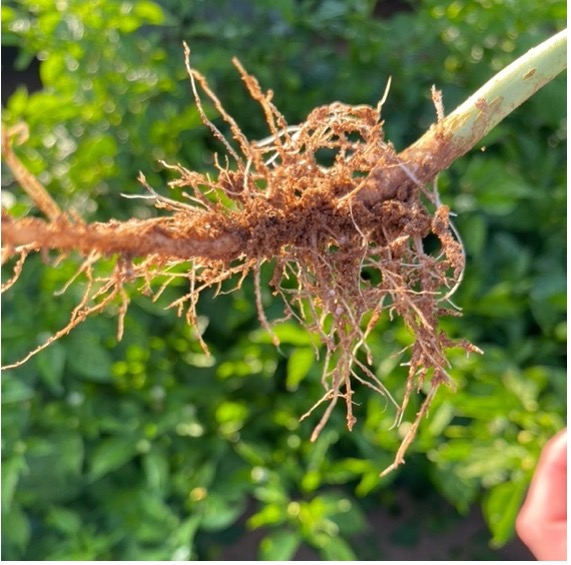
We would all like to just say a massive thankyou to Struan Moore-Gordon and his family for organising this whole trip and making it all possible, looking after us for the 3 weeks we were out and making us feel so welcome and at home.
Also, a massive thankyou to all the farmers from Gwaai farm, Pinfeilds farm, Hidden Valley, Foxhill farm and Hurkuru hatchery, for taking the time to give us detailed tours around all their holdings, it was such an eye opener to see how productive it was out in Zimbabwe and very interesting to so all the different things the county is known for producing. And finally, a massive thankyou to John Cameron for offering financial support and helping enable us to get out to Zimbabwe to see everything it had to offer.
It was the trip of a lifetime and certainly something that the three of us will never forget.